|
|
|
|
|
Sembcorp’s priority is to deliver long-term value and sustainable returns to our shareholders. As a multinational enterprise and a public listed company, we understand that there is a complex value chain to which Sembcorp belongs and that our wider responsibility incorporates sustainability issues. We fully recognise that these issues may be outside the traditional view of corporate activity, but as the global business landscape evolves, managing these issues is increasingly viewed as vital in maintaining companies’ “license to operate” from society and their stakeholders.
This widening role of business is taken seriously by Sembcorp and we believe our commitment to excellence and continuous improvement in our health, safety and environment (HSE) performance as well as governance and human resources builds and protects the value of our business.
In our management of sustainability and governance, many issues are directly managed at the Group level with the support and input of each of the business units. Examples of these include our corporate governance programmes, risk management and mitigation strategies, group-wide HSE, as well as community investment initiatives. A number of commitments external to the company have also been undertaken such as membership of the chemical sector’s Responsible Care initiative, and an anti-corruption declaration with a well-recognised and respected non-governmental organisation in Singapore.
The approach taken by Sembcorp to manage sustainability is intended to benefit our shareholders, other key stakeholders and the communities in which we operate, on a global basis. In early 2010 we were recognised for our efforts by being included in the ‘Global 100: Most Sustainable Companies in the World’ published by Corporate Knights and the Global Research Alliance, a leading sustainability publication and research collaboration. Launched in 2005, the Global 100 is announced each year at the sidelines of the World Economic Forum.
With customers and operations around the world, Sembcorp is an international company. Our four main operating units comprise Utilities, Marine, Environment and Industrial Parks. As our Marine business is separately listed and reports its activities in its own annual report, this report will primarily cover the other three strategic business units (SBUs). Data for our key performance indicators (KPIs) for these SBUs has been tracked and reported in the areas of environment, health and safety, human resources and community investment. Aside from this chapter, information on the company’s corporate governance, risk management and mitigation strategies, and investor relations which are part of the wider ambit of sustainability issues, may be found in the relevant chapters under the Environmental, Social and Governance Review section of this annual report.
The following sustainability report addresses the activities and data that fall within the company’s financial year for the period from January 1 to December 31, 2009. Sembcorp has included aspects of sustainability in our annual report since 2001 and these issues were last reported for the financial year 2008. |
|
As part of the development of our sustainability reporting systems, we have begun to implement the Global Reporting Initiative (GRI) G3 reporting principles and framework and aspects of the GRI Electric Utility Sector Supplement on a voluntary basis. Our aim is to work towards providing readers with an accurate, complete and reliable report that contains meaningful information on how we manage sustainability issues in our specific business sectors. The disclosure processes will also allow our stakeholders to view our progress over time. In our reporting, Sembcorp will also consider the principles of the GRI in terms of materiality, stakeholder inclusiveness, sustainability context, completeness, accuracy and comparability. |
|
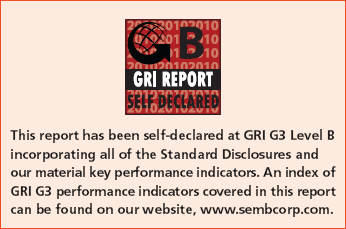 |
|
|
|
|
We have tried to incorporate as much data as possible
from our ongoing operations and the scope of this report includes reporting on our majority owned business units, particularly our operations in Singapore and the UK. While reporting boundaries are based on currently available data from these operations, reference has also been made to other joint ventures and associates where appropriate. Where data is unavailable or has been excluded, this has been clearly stated, and data measurement is in line with GRI G3 recommendations for our chosen indicators. Sembcorp is committed to continuous improvement and aims to expand the scope of the report in the future. Our target for our ongoing reporting development is to incorporate reporting on all those SBUs which Sembcorp has a majority stake.
Identifying, monitoring and managing material issues that we believe are relevant and significant for
the company and its stakeholders is an ongoing process at Sembcorp. We aim to regularly review these issues, bearing in mind that these are dynamic and can change
over time and across different geographical areas.
In general, Sembcorp’s management and monitoring of sustainability issues is based on a risk management approach. However, we also recognise that there are
tremendous opportunities to actively invest in sustainable business lines. Using our integrated group strength, we apply proven technologies to produce energy in greener ways, create innovative solutions for clean, sustainable water and help manage resources through the treatment and recovery of recyclables from waste. In this way, we not only do our part to limit the impact of our activities on the environment while staying competitive, but also help our customers to do the same.
At Sembcorp, we also recognise the very useful role which employee engagement and two-way communication channels can play, not only in determining
our sustainability-related risks but also in identifying areas for future improvement. Sembcorp maintains a
whistle-blowing scheme and also provides our employees
with confidential feedback channels. To promote a sustainability culture within the Group, employee appraisals take into account HSE performance. Our
employees are also encouraged to contribute innovative
ideas and suggestions to improve workplace practices, products and services, including their HSE impact.
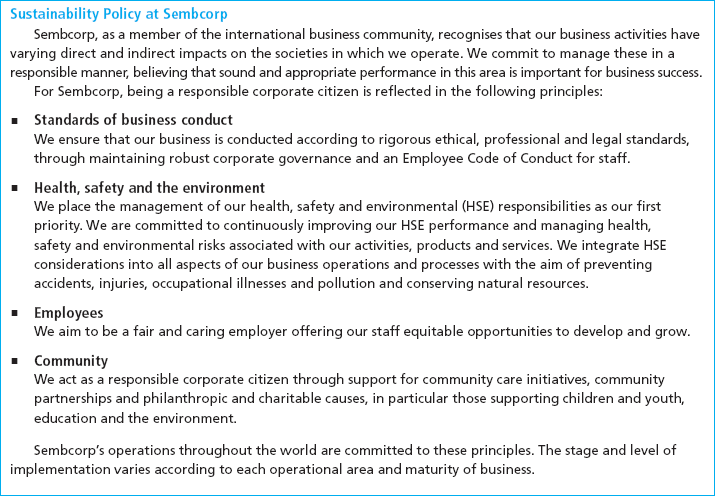
Our efforts to engage our internal stakeholders in the practice of sustainability are also supported by our engagement with other companies and organisations, ranging from site and industry-specific groups to organisations with a much wider agenda.
Sembcorp is a founding member and supporter of the Singapore Compact for Corporate Social Responsibility, a national society promoting sustainability issues in Singapore and a participant in the United Nations Global Compact.
At the industry level, Sembcorp participates in the Responsible Care voluntary initiative, which is endorsed by the Singapore Chemical Industry Council (SCIC). This encourages members to adopt 10 guiding principles for a safer chemical industry through the six management practices of employee health and safety, distribution, pollution prevention, process safety, product stewardship and community awareness and emergency response. Sembcorp is also a member of the Sakra Island Community Awareness Group (SICA), which seeks to promote community awareness and a standardised management practice code for emergency responses among companies located in the Sakra cluster on Singapore’s Jurong Island.
In 2009, Sembcorp signed a regional declaration on anti-corruption in an initiative led by the Singapore Institute of International Affairs (SIIA) a regional think-tank in Southeast Asia.
In the UK, Sembcorp is currently one of around 50 organisations in the world to have achieved the British Standards Institute (BSI) Management Systems BS25999 standard for business continuity management. In 2009, the Protection business unit also worked with BSI to promote the new standard to the wider business community and took part in external education events. |
|
Due to the scale of Sembcorp’s operations, our supply chain is a complex one. Our commitment to issues such as HSE performance dictates that our sustainability policies should deliver wider beneficial effects for all stakeholders who are part of our value chain.
As an integrated utilities provider, Sembcorp directly uses primary resources, whilst other parts of the business operate and maintain or manage facilities and buildings, treatment processes, machinery and people. Sembcorp already works closely with our suppliers, business partners and contractors to promote issues such as health and safety to encourage our contractors to practise pollution control at source and waste minimisation. For each contract that is awarded by Sembcorp, an assessment of the contractor’s general capability is undertaken to ensure that the delivery of the project will be in line with our health, safety and environment policy. We also work collectively with our suppliers to actively identify and improve upon performance in these areas via platforms such as contractor HSE committee meetings, safety induction programmes as well as vendor performance audits. |
|
Sembcorp also owns and operates facilities which supply products and services to industrial customers. We understand that many of our multinational clients are in the process of developing and integrating their own sustainability programmes and Sembcorp aims to help them improve their own performance by being a responsible member of their supply chain.
Constructive dialogue with our stakeholders is an important tool for Sembcorp to understand our internal and external business environment and deliver
the right products, services and information to the right groups at the right time. Our engagement processes, including identification and prioritisation, broadly reside at the operational level with some oversight at Group level, but stakeholder engagement involves all of the issues highlighted in this report.
Our main stakeholder groups can be identified as
regulators (including diverse entities such as the Singapore Stock Exchange and the Energy Market Authority), financial institutions, shareholders and other investors, suppliers, customers and communities in which we operate.
As part of ongoing efforts to elevate the importance of engagement, we have carried out a pilot stakeholder engagement programme using the AA1000 Stakeholder Engagement Standard as the basis for its methodology. This standard is a framework for designing, implementing, assessing and assuring the quality of stakeholder engagement and will assist Sembcorp to improve transparency, reporting and accountability over time.
The purpose of the exercise is to engage a target number of internal and external opinion formers and discuss what they feel sustainability should mean for Sembcorp. We hope to add to the overall depth and credibility of stakeholder engagement at Sembcorp and relevant findings from the exercise could also provide some indicators to develop and include in the future.
Through these internationally recognised standards
and other formal engagement processes, such as our investor relations programme, we hope to align relevant issues with our overall strategy and use this process as part of our ongoing target setting.
In line with our continual drive for innovation and to widen our sustainable business portfolio, the development of sustainable or ‘green’ business lines has become a growing part of our ongoing core businesses. We foresee sustainable products and services delivering an additional competitive edge and enhancing our reputation as a responsible and responsive company. Sembcorp’s sustainable business operations include:
At Sembcorp’s operations in the UK, we operate a 35-megawatt renewable energy power station using sustainable wood for fuel (see case study below), enough to power 30,000 households.
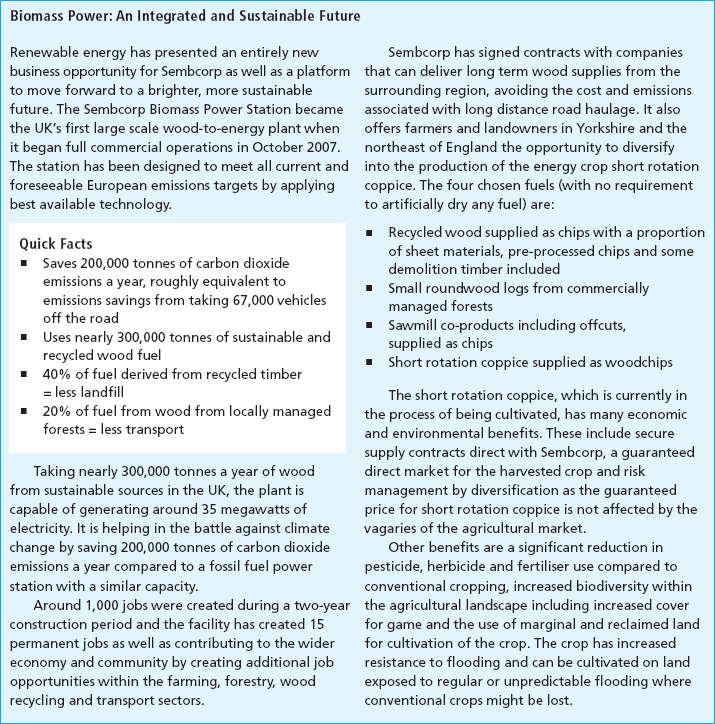
Sembcorp was the first commercial importer and retailer of natural gas in Singapore and the first company to supply and retail compressed natural gas directly to motorists. We import 341 billion British thermal units of natural gas per day from West Natuna in Indonesia and starting in late 2011, we will import an additional 90 billion British thermal units of gas per day.
Sembcorp continues to seek greater efficiency and lower emissions in our power, steam and desalination operations in Singapore, China, the UK, the Middle East and Vietnam through the use of technology.
In Vietnam, we make use of combined cycle gas turbine technology, where waste heat from gas turbines is used to create steam to generate additional electricity via steam turbines. This enables us to generate more electricity from each unit of fuel input. In addition, we operate cogeneration plants in China, Singapore and the UK. Cogeneration refers to the production of both electricity and steam from a single fuel input at a facility located near the consumer. Considered the most efficient use of fuel, cogeneration improves the overall recovery of heat and also saves on fuel needed to produce heat or steam in a separate unit. Cogeneration plants also generate substantially lower emissions compared to conventional power plants.
We also co-own and operate a combined power-and-desalination facility in the UAE with an 893 megawatt power generation capacity and a seawater desalination capacity of 100 million imperial gallons per day. This plant captures heat created as a by-product of the power generation process which might otherwise have been lost in the form of flue gas, for use in seawater desalination. In addition, we are building a combined power-and-desalination plant in Oman with a gross power generation capacity of 490 megawatts and a seawater desalination capacity of 15 million imperial gallons per day.
Through Sembcorp’s range of services, waste that would usually be disposed of in landfill and incineration facilities is diverted for recycling. We also have capabilities in advanced waste treatment and resource recovery, including composting and waste-to-energy recovery. Sembcorp’s award-winning environmental arm in Australia, SITA Environmental Solutions is the leader in the development and operation of advanced resource recovery facilities.
Our waste-to-resource facilities in Singapore extract recyclables from waste collected through our collection arm, which is the leading operator in Singapore serving four out of the nation’s nine municipal sectors. Sembcorp also operates a construction and demolition materials recovery facility in Singapore capable of processing 300,000 tonnes of construction and demolition waste per year. Timber, hardcore and fines, as well as ferrous and non-ferrous metals are recovered during the sorting process. Furthermore, the complete range of waste paper recycling services is offered from collection, sorting and baling to bulk supply of recovered paper to paper manufacturers. With more than 20 years of experience in waste paper recycling, we have an extensive network collecting some 300 tonnes of waste paper each day. |
|
In Singapore and China, Sembcorp is a pioneer in industrial wastewater treatment and water reclamation. Sembcorp’s facilities are capable of treating high organic concentration and high salinity industrial wastewater which can be 20 times more concentrated than municipal wastewater and 1.5 times more saline than seawater. In 2009, we increased our integrated wastewater treatment capacity in Singapore by over 50% with the opening of a 3,000 cubic metres per day industrial wastewater plant utilising membrane bioreactor technology. Sembcorp is the only company in Singapore to have successfully applied this advanced technology for the treatment of industrial wastewater, which allows our plants to occupy a smaller plant footprint compared to a conventional aerobic treatment system, yet produce effluent of a consistently high quality with lower energy consumption, minimal chemical usage and a reduced amount of sludge.
Sembcorp was also the first company to reclaim secondary effluents from industrial wastewater, applying dual-media filtration, microfiltration, reverse osmosis and ion exchange technologies to produce high purity demineralised water and high grade industrial water for supply to its customers. Today, Sembcorp’s supply of demineralised water and high grade industrial water
to customers is substantially derived from reclaimed water. Our ability to integrate wastewater treatment, water reclamation and water supply in a “closed loop” minimises liquid discharge, conserves potable water supplies and promotes a sustainable water supply.
The Sembcorp NEWater Plant, designed, built, owned and operated by Sembcorp, is Singapore’s largest plant producing treated used water that has undergone stringent purification and treatment process using advanced dual-membrane and ultraviolet technologies. It began operations in July 2009 and when fully completed in mid-2010, will be one of the largest water recycling plants in the world, producing 228,000 cubic metres per day.
Sembcorp’s Industrial Parks business applies an integrated approach to township development, providing world-class manufacturing space coupled with a sustainable urban environment.
In May 2009, the business entered into a joint venture with Yanlord Land Group and Surbana Land to develop the Sino-Singapore Nanjing Eco High-Tech Island in Nanjing, China. The development will offer approximately 6,000,000 square metres of gross floor area for prime commercial, industrial and residential use. When completed, it will house many of the world’s leading technology companies. The Eco High-Tech Island will be progressively developed and will provide a platform for the sustainable development of high-tech, smart industries and services. This commercially-driven project will focus on the growing importance of achieving a balance between continued technological progress and environmental preservation.
Research and development plays an important role in strengthening Sembcorp’s sustainable capabilities. One such example in 2009 was the partnership between
Sembcorp and the Nanyang Technological University’s Nanyang Environment and Water Research Institute (NTU-NEWRI) to jointly explore the application of a new system for the treatment of complex industrial wastewater. Sembcorp and NTU-NEWRI will work together over the next three years to explore a novel treatment technology aimed at removing recalcitrant organic matter from wastewater. The process models nature’s way of cleaning the water and it is hoped that the technology can be more competitive than other technologies.
In June 2009, Sembcorp signed a technical assistance agreement with local water technology companies United Envirotech and Memstar to form a pilot testbed for a new high environmental performance system to treat industrial wastewater and reclaim water. The system will be the first in Singapore to apply membrane distillation technology for the treatment of industrial wastewater and water reclamation. The system will aim to maximise the reclamation of clean water from treated effluent and make progress towards achieving affordable zero liquid discharge solutions. The new testbed is in line with Sembcorp’s efforts to commercialise promising new sustainable technologies and help industrial sites and cities minimise discharge into waterways.
In the past year, Sembcorp has received a number of awards, both nationally and globally for its efforts to promote and practice sustainability.
Sembcorp was one of two Singapore-headquartered
companies included in the ‘Global 100 Most Sustainable
Corporations in the World’ list. The list, published annually by Corporate Knights, a magazine for “clean-capitalism”, applies environmental, social and governance measures to demonstrate that “the most sustainable companies attract the most capital and earn the best returns…squeeze[ing] more wealth from less material resources while honouring the social contract.” Key assessment parameters include energy, carbon, water and waste productivity, leadership diversity, percentage tax paid, sustainability leadership,
innovation capacity and overall transparency. Sembcorp was ranked 78th on the list.
Sembcorp was honoured by the Singapore Chemical Industry Council (SCIC) with a gold award in the ‘Community Awareness and Emergency Preparedness’ code category and two achievement awards in the ‘Employee Health and Safety’ and ‘Pollution Prevention’ code categories at the Responsible Care Awards 2009. The awards were conceived to honour companies who have incorporated Responsible Care Management Practices into their operations, and to recognise those with exemplary performance in maintaining high health, safety and environmental standards.
Sembcorp won four silver Workplace Safety and Health Performance Awards at the Workplace Safety and Health Performance Awards. The annual awards are presented by the Workplace Safety and Health Council in collaboration with Singapore’s Ministry of Manpower to give recognition to organisations that have performed well by implementing sound health and safety management systems. The four silver awards were received by Sembcorp Gas, Sembcorp Cogen, Sembcorp Industries’ SUT Division and collectively by Sembcorp’s Sakra Island Carbon Dioxide and PPU Division as well as Sembcorp Air Products (HYCO).
Sembcorp’s waste collection unit received a commendation award from the National Trades Union Congress in recognition of our strong commitment to growing a constructive partnership between
the company and the union, and also for our continuing focus in skills upgrading, work safety and employee welfare.
Sembcorp UK’s vastly experienced Protection Team, which protects more than £14 billion of industrial assets in the UK was recognised by the UK’s Chemical Industries Association (CIA) by being named the winner of the CIA 2009 Awards in the Professional and Engineering Supplier category. The award recognises suppliers whose services allow chemical manufacturers to concentrate on their
own area of expertise.
Sembcorp’s Protection business is based at the company’s Wilton International site on Teesside in the UK and supplies a wide range of services to customers, from world class fire fighting and chemical spill protection, to emergency planning, site security and business continuity expertise.
Sembcorp’s Australian environmental arm, SITA Environmental Solutions (SES), won the inaugural Frost & Sullivan Asia Pacific Industrial Technologies Award for
‘Waste Management Company of the Year’. SES was selected by Frost & Sullivan, a global growth consultancy, for the award given its excellence in waste management and treatment, and its active application of progressive technologies particularly in areas like waste-to-resource. This award provides a clear message that SES’ commitment to developing sustainable and innovative advanced resource recovery practices is the Asia-Pacific benchmark for all recycling and waste management companies operating in this region.
Sembcorp’s waste collection unit was named the winner of Distinguished Defence Partner Award 2009 by Singapore’s Ministry of Defence for our continuing support and contributions towards operational readiness for national defence.
HSE issues are closely linked with Sembcorp’s long-term business success. HSE issues have been identified as material factors in terms of their potential impact on our main business operations. Clean air and climate change, water, waste and the health and safety of our employees and business partners are areas where we have focused our sustainability efforts and resources.
Under our Group HSE policy, which can be viewed on our website at www.sembcorp.com, Sembcorp views HSE issues as its first priority. This section
of the report will provide information on how the Group pro-actively manages impacts arising from
its operations.
We continue to be guided by four HSE main principles which include: |
|
• |
Implementing internationally recognised HSE management systems such as ISO14001 and OSHAS18001, as well as our own additional indicators such as SCU 5/0. |
• |
Actively investing in financially viable sustainable business lines, which form part of our core operations. |
• |
Continuous improvement to enhance HSE performance of our processes, products and services (incorporating feedback, audits and innovation to strengthen the functioning of our management systems). |
• |
Working closely with our business partners and seeking active engagement to promote mutual HSE performance improvement and positive impacts. |
|
|
Sembcorp’s culture of HSE involves everyone associated with the company. This approach of shared responsibility means that employees and business partners, including contractors, must all take ownership of our day-to-day health, safety and environmental performance, and meet the standards that we expect.
Our Group HSE office is the driver of our management systems and co-ordinates our global HSE efforts. HSE management committees and associated reporting structures have been established for the effective management of HSE issues with the express
purpose of setting long-term HSE objectives and targets and complying with the regulatory requirements and voluntary guidelines and initiatives.
An example of this structure is our operations on Jurong Island in Singapore, where the HSE Committees are structured at two levels. The main HSE Committee comprises all heads of department while the HSE Sub-Committee comprises members from the respective operating plants on Jurong Island. The committees are responsible for monitoring and reporting results, ensuring continuous improvement, enhancing effective two-way communication, and engaging with staff and maximising their involvement. The sub-committee comprises representatives from various disciplines, not just HSE, and there are at least three employees and three management representatives at each committee level. During the 2009 reporting period monthly sub-committee meetings were held, whilst the main HSE committee met quarterly.
Similar structures are used at our various business units to ensure that HSE is always a high priority.
From mid-2009, a Sembcorp Contractors’ HSE Committee for Utilities in Singapore was initiated to promote wider co-operation in achieving and maintaining HSE performance amongst all contractors working with the company.
This important addition to our HSE management systems at Sembcorp has set a series of targets which include: |
|
• |
Carrying out inspections to highlight gaps or deficiencies in HSE control. |
• |
Keeping abreast of developments in new technologies, legislative changes and the introduction of new products. |
• |
Jointly organising safety promotion activities to generate HSE awareness among workers. |
• |
Contributing safety suggestions and participating actively in areas that would improve the overall safety performance of contractors as well as more widely at Sembcorp. |
• |
Investigating any accident, incidents or near-misses relating to HSE and recommending counter measures to prevent recurrence. |
|
|
As a key player in the energy sector, Sembcorp is mindful of our impact on clean air and climate change. Sembcorp works towards limiting and managing environmental impact by improving the efficiency and performance of our operations.
Emissions and energy usage are monitored and the levels of carbon dioxide emitted by some of our Utilities operations have been reported on for a number of years with a view to limiting emissions. For the purpose of this report, data is from our wholly or majority owned units in Singapore and the UK unless otherwise stated.
Total carbon dioxide emissions in Singapore increased from 2,789 to 3,100 kilotonnes due to the increase in the production of steam during the reporting period. In the UK there was a marked reduction in carbon dioxide emissions from 1,065 kilotonnes to 810 kilotonnes. This was mainly due to a significant increase in the use of natural gas and decrease in the use of coal as a new gas turbine and heat recovery steam generator was brought into service.
In addition to tracking direct carbon dioxide emissions, we monitor the energy usage of our Utilities operations. Electricity consumption from our Utilities operations increased slightly by 1.2% from 131,808 gigajoules to 133,400 gigajoules for the year.
We also track our Utilities operations’ primary energy sources usage. Natural gas continues to remain the largest constituent of our primary energy sources (all measurements have been expressed in gigajoules for ease of comparison).
As a result of our continued efforts, and the use of closed-loop systems in Singapore that reuse and recycle water, we have, for three consecutive years, reduced our use of potable and raw water. Our total potable and raw water consumption in the UK and Singapore fell by 35% in 2009.
In addition to tracking our own water use in our operations, Sembcorp’s wastewater treatment activities also treat industrial effluent generated by our customers to reduce their impact on the environment.
With HSE issues being a top business priority, Sembcorp launched the internally driven SCU 5/0 initiative in 2006. This encompasses the five goals of zero injury, zero spill, zero non-compliance, zero hazardous release and zero unplanned shutdown. The initiative provides a common platform across all of our Utilities operating sites and requires all employees to identify hazards and gaps in activities and eliminate them. Employees at all levels are encouraged to participate in the discussion of HSE issues arising in their course of work.
The campaign has been effective and in 2009 the “price of non-conformance”, our internal measurement indicator for the imputed monetary cost of lapses relating to the five indicators, decreased by 38%. Since the campaign was started over five years ago, the overall price of non-conformance has decreased by 90%. |
|
SCU 5/0 was introduced to our UK operations in 2009 and the data collected will form part of the wider HSE monitoring and management systems at Sembcorp.
For 2009 we have been able to extend the scope of our accident and injury rate reporting. Beginning last year in Singapore, we started to use accident frequency rates (AFR) and accident severity rates (ASR) in accordance with the tracking criteria set by Singapore’s Ministry of Manpower. The safety performance from our UK operations is now incorporated with data from our Utilities operations in Singapore. Our Environment operations’ safety performance in Singapore is also reported on separately.
Our Utilities operations had four reportable cases in 2009, two in the UK and two in Singapore. For the ASR, our Utilities operations reported 64 man-days lost per million man-hours worked in 2009, compared to zero man-days lost in 2008. One of the accidents, which accounted for 57 days of lost time, was a cycling accident that took place when an employee was travelling between operations sites in our Jurong Island facilities in Singapore. We will continue to strive for zero accidents and believe our SCU 5/0 initiative will help us to achieve this.
In terms of prevention initiatives, Sembcorp’s operations in the UK ran a successful seminar on process safety for managers and engineers taking several external industrial incidents as learning examples. The focus was on human behavioural aspects of the accident and the interface with equipment and processes. Attendees gained insight as to how they could take such factors into account in the design and operation of facilities.
For our Environment business in Singapore, we saw an increase in the AFR and ASR compared to 2008. This was mainly due to two industrial accident cases that led to an extended number of days away from work, along with a decrease in the number of man-hours worked by 33% due to a divestment of part of the business. |
|
Safety is important to us and our Environment business has taken preventative action to improve its AFR and ASR levels. This includes additional “toolbox meetings” with management and employees to cover the importance of health and safety. Spot inspections at operational sites were also conducted more frequently and new guidelines relating to the use of safety equipment were implemented. |
|
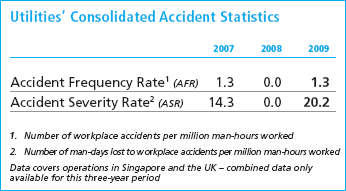 |
|
|
|
|
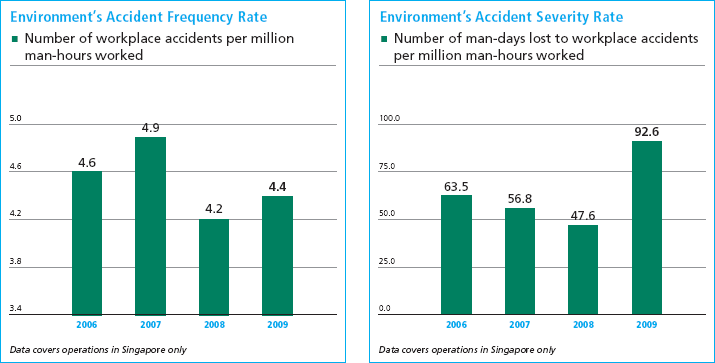 |
|
With a relatively large number of commercial vehicles in use, a considerable amount of driving is undertaken in the course of the year by our waste management unit. Hence, a key indicator for safety is the unit’s vehicle accident rate. In 2009, there was a fall in the total number of vehicle accidents.
Our ongoing preventive and corrective measures include counselling, internal disciplinary systems jointly spearheaded by operations and human resources, with the direct involvement of the union, to improve driver selection and orientation programme. We also have awards for drivers achieving three years of traffic accident-free service with the company.
The HSE Accident Incident Management System, a web-based application that tracks and reports incidents and accidents at the Utilities operational facilities in Singapore, was launched in 2009. The system tracks the status of reported incidents and accidents and creates a useful database for analysis and learning. Based on two HSE procedures, hazard identification, risk assessment and risk control, and incident and non-conformance reporting, it is a positive step forward in our HSE management systems.
To strengthen its HSE performance, Sembcorp joined the Singapore branch of Responsible Care in 2008. An initiative of the global chemical industry, Responsible Care signatories must commit to implementing the guiding principles and management codes of practice. At the Responsible Care Awards 2009, Sembcorp won a gold award for ‘Emergency Preparedness and Community Awareness Code’ and two achievement awards under the ‘Pollution Prevention Code’ and ‘Employee Health and Safety Code’ categories.
As a signatory to Responsible Care in Singapore, Sembcorp has committed to: |
|
• |
Implement all relevant components of the Responsible Care codes of management practices in Singapore. |
• |
Implement and describe specific company initiatives on HSE and community openness. |
• |
Strive for continuous improvement in HSE performance and standard with zero injuries, incidents and waste. |
• |
Regularly brief employees on Responsible Care objectives, processes and results as part of its own HSE activity and improvements; supported by SCIC to allow employees to represent the industry as ambassadors. |
• |
Consider and give weightage to HSE performance reflected in the Responsible Care Guiding Principles and processes when selecting suppliers of materials or services. |
• |
Broaden the influence of Responsible Care to the users of chemicals by implementation of product stewardship by all employees. |
• |
Submit self-assessment and key performance indicator forms annually. |
|
|
Sembcorp’s Utilities operations in Singapore launched an HSE e-learning platform in mid-2009. This project was triggered by the need to provide an alternative learning environment for staff to ensure HSE skills are regularly upgraded without the need to spend a great deal of time away from office. At present, the range of modules includes safety inductions, hearing conservation and scaffold safety amongst others.
The HSE department also conducted a series of roadshows to promote the initiative as well as to orientate staff on the use of the system. Harnessing innovation and technology, the interactive web-based lesson content is interspersed with informative videos and energetic presentations, animations, graphics and interactive exercises. Employees are expected to demonstrate clearly specified competencies by the end of the session and are able to review their personal learning records.
HSE teams also collaborated in cross audits at Utilities operations in Singapore, UAE and the UK. The audits are undertaken to develop expertise and share best practice within the different operating environments at Sembcorp.
HSE staff from our Utilities operations in Vietnam visited Utilities operations in Singapore to learn and share HSE best practices during a major inspection in
Singapore in mid-2009. Officers from the Group HSE
Office also visited our water operations in Shenyang, China, to assess and understand the site’s existing HSE
management systems and identify and recommend areas
for improvement. The two-day programme allowed both teams to learn and share best practices and discuss
how management systems may be continually enhanced
in order to achieve improvements. Collaborative visits and cross audits will continue as part of our overall efforts to derive opportunities in HSE performance consistent with Sembcorp’s HSE Policy. |
|
A main principle of our sustainability approach is to implement internationally recognised management standards. To this end, 2009 saw a great effort to implement ISO 14001:2004 certification across the entire Utilities business in Singapore.
Sembcorp Industries – SUT Division, a unit of our Utilities business, has held ISO14001 certification since 2001 but with a view to continuous improvement,
we committed to implementing this certification with a
broader reach and more integrated approach. Therefore,
our Singapore Utilities operations are currently in the process of seeking certification covering all Utilities operations in Singapore.
As the leading management player in Singapore, Sembcorp’s Environment business provides services that aim to reduce waste going to incineration or landfill facilities. We also promote waste reduction by providing separate bins for recyclables as part of our waste collection service to municipal customers.
In line with our business focus to reduce waste, we are actively developing differentiating know-how including waste-to-resource capabilities.
At Sembcorp, we recognise that our employees are our most vital assets and a key stakeholder group. We believe in providing a fair, diverse and inclusive workplace for our employees. We are committed to continuous improvement in our human resources and people development approach and practices, and working together with our employees to achieve this aim.
The scope of this section of the report covers the activities of the Utilities, Environment, Industrial Parks, Design and Construction and Mint business units. We have covered key data relating to our main Singapore operations and our various overseas units in China, Vietnam, the UK, the UAE and Oman as well as our overseas industrial parks. If there is any deviation from this scope it is noted under the individual indicator.
Sembcorp engages our employees through a variety of channels on areas such as group financial and business performance, ethical standards, employee feedback mechanisms and information provision.
During the business performance review cycle, senior management, including the Group President & CEO, attend town hall style briefing sessions and roadshows. These sessions help to give employees a better understanding of strategy, performance and future direction of the company.
In addition, a confidential employee feedback system is available to all staff. In line with our commitment to high ethical standards and good corporate governance practices, we encourage all employees to report any possible improprieties and maintain a group-wide whistle-blowing policy.
Relevant, up-to-date information on human resource policies, procedures, legislation and best practice is made available to most employees via the company intranet. The system, which offers easy access with search facilities, is available to most of Sembcorp’s employees. A handbook is made available to employees who do not have access to the intranet.
Communicating corporate updates, such as press releases and a bi-monthly employee e-newsletter, is done via email blasts to staff. At the country level some business units hold quarterly learning and sharing sessions, as well as senior manager briefings.
Socially, Sembcorp encourages employees to participate in events that are run regularly throughout the year. Most of the business units involve staff in sports and recreation club activities which can take the form of festive parties, team sports and annual family days.
The Group subscribes to the Principles of Fair Employment in Singapore and has endorsed the Employers’ Pledge of Fair Employment Practices formulated by the Singapore Tripartite Alliance for Fair Employment Practices. Sembcorp’s commitment is encompassed in the incorporation and implementation of these principles in our human resource management practices at the global level.
The fair employment principles incorporate a commitment to: |
|
• |
Recruit and select based on merit, such as skills, experience and ability, regardless of age, race, gender, religion or family status. |
• |
Treat employees fairly and with respect and implement progressive human resource management systems. |
• |
Provide equal opportunities for training and development based on employees’ strengths and needs, to help them achieve their full potential. |
• |
Reward fairly based on ability, performance, contribution and experience. |
• |
Abide by labour laws and adopt tripartite guidelines which promote fair employment practices. |
|
|
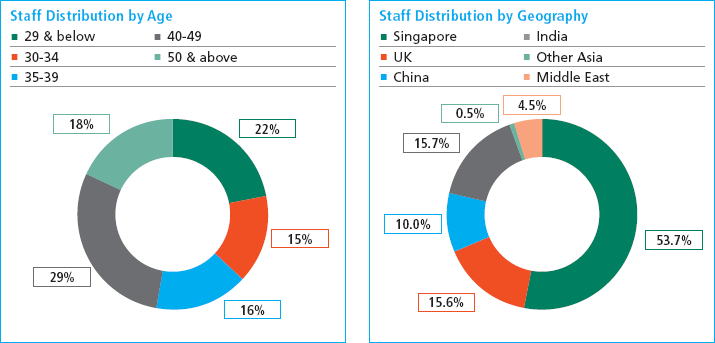 |
|
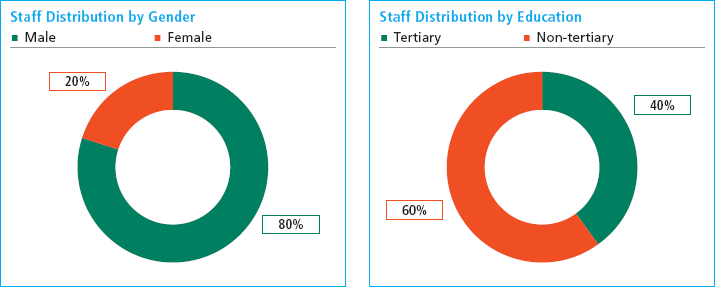 |
|
Sembcorp fully supports basic principles of human rights. We have several policies in place relating to the support of these, including a set of fair employment practices, a grievance and harassment policy and a recruitment and selection policy. We also have strict control procedures in place for contractors who are working for Sembcorp.
Sembcorp respects labour laws within each of the countries we operate in. Through our policies and the planning and administration of our employment practices, we are confident that our operations are not exposed to issues such as child or forced labour. |
|
All Sembcorp employees have freedom of association within the confines of the legal and regulatory environment for each of the countries that we operate in. At the end of 2009, there were 787 unionised members working at Sembcorp, covering 27% of our workforce. Sembcorp employees were also covered under five separate collective bargaining agreements with our unions in Singapore and the UK. |
|
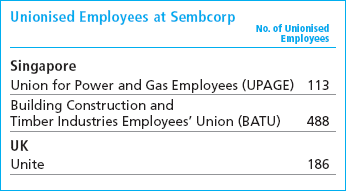 |
|
|
|
|
Sembcorp maintains ongoing exchanges with employee unions. In 2009, we met the Union for Power and Gas Employees (UPAGE) for discussions regarding employee benefits for our Singapore Utilities staff, and renewed a three-year collective agreement. Sembcorp’s Utilities business also worked closely with UPAGE in its membership drive and supported it in its implemention of the work skills qualification framework for the power and gas industry.
At Sembcorp UK, discussions with Unite, the UK’s biggest union, are conducted in line with our collective agreement (the ‘Together Agreement’) applying agreed Partnership Principles. Over 91% of employees in this business unit are covered by the collective bargaining agreement.
In late 2009, Sembcorp Environment divested its conservancy services, commercial cleansing and car park management units in line with its strategy to focus its business on waste-to-energy products. The entire divestment process was undertaken in parallel with an engagement and consultation exercise with the Building Construction and Timber Industries Employees’ Union (BATU) and the Deputy Executive Secretary and Principal Industrial Relations Officer of BATU were present at closed-door communication sessions held for
affected staff. All employees affected by the divestment were offered continued employment under the new business owner based on the same terms and conditions of employment under Sembcorp. This carefully managed process ensured that 99% of employees were transferred to the new business. In appreciation of past service, the affected employees were offered an ex-gratia payment payable upon the completion of three months’ service with the new business owner.
In addition, as an outcome of Sembcorp’s regular dialogues with its respective unions, Sembcorp’s Singapore operations supported an extended retirement policy with UPAGE and BATU, offering continuing employment to staff who are past the statutory retirement age of 62. |
|
As the success of a corporation is driven by the calibre and the performance of its employees at all levels, Sembcorp makes it a priority to continually develop its workforce. Through our career development, education, talent management and leadership programmes, we offer our employees a range of avenues for personal and professional development. |
|
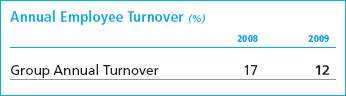 |
|
|
|
|
In 2009, the group continued to invest in competency building for our employees, spending S$5.54 million on training. Our learning and development programmes factor in issues such as succession planning and turnover rate of employees. With around 3% of the workforce due for retirement in the next five years, it is a priority to enhance the skills levels of our employees to ensure a smooth succession.
Our training and development programmes include: |
|
• |
Working with local educational institutions, Sembcorp has developed and conducted specialised technical courses for the Utilities business. |
• |
Capable leaders are vital to the success of any corporation and our unique talent management and development system, called the ‘Sembcorp Leadership Competencies’ system, defines the qualities and performance expectations of a Sembcorp leader. This set of competencies details the ways in which Sembcorp leaders should act and respond to achieve extraordinary business success. We also send our managers on courses to enhance their presentation, negotiation, communication and coaching skills, as well as on courses on building and leading high-performance teams.
To continually develop our executives’ leadership, strategy and management skills, our senior staff also attend executive education programmes at prestigious institutes such as the Harvard Business School, INSEAD and the Temasek Business Leadership Centre. |
• |
Job rotation and overseas postings are another way in which we offer employees vital experience in other cultural settings and exposure to practical operational issues first-hand in other Sembcorp business units. There are currently 38 employees posted to various overseas businesses. Internships also provide Sembcorp’s scholars with practical experience and essential operational exposure during their studies. |
• |
Sembcorp also runs on the job training for its employees. Examples of this include the National Skills Recognition Scheme certification courses undertaken by operations staff. |
• |
This year saw the launch of the health and safety e-learning initiative. The project was triggered by the need to provide an alternative platform for staff to participate in HSE learning and skill upgrading without the need to spend time away from office or have prescribed periods for training. The e-learning initiative was led by the HSE team and has proved successful with 58 employees having undertaken the training to date. |
• |
Along with education and training opportunities, Sembcorp offers employees the opportunity to attend, present and participate in conferences on a local and international basis. As an industry leader in many sectors of our business, we encourage knowledge and best practice sharing through these platforms. |
|
|
Sembcorp’s employee performance appraisal system includes a feedback process that identifies development areas and allows employees to comment on their own contribution throughout the year. It incorporates future objectives to ensure that all of our employees’ outputs are aligned to the performance of the business. In addition, we apply 360-degree feedback in assessing mid-level and senior managers. Under this system, feedback from a range of superiors, colleagues and other partners are incorporated into managers’ development plans, helping them build a profile of essential competencies needed to improve their professional performance and lead their teams successfully.
Sembcorp offers competitive base pay packages that are based on country-specific conditions. Long-term
employee performance incentives are linked to sector practices and benchmarks and rewards are based on the performance of the Group, company and individual. Rewards include annual salary increments, annual performance bonuses and longer-term incentives.
Share-based incentives remain a key component of the Group’s pay structure to motivate staff and align longer term performance objectives. These are administered by a board nominated committee. Since 2007, no share options have been granted as these have been entirely replaced with Restricted Stocks
of an equivalent fair value. The Restricted Stock Plan is used for directors and employees of Sembcorp Industries and our subsidiaries whereas the Performance Share Plan is aimed primarily at key executives of the Group.
All employees are eligible for comprehensive insurance coverage on a global basis. They can join our Private Medical Insurance Scheme where the Company meets the cost of employee membership and allows employees to include eligible dependants. Other insurance schemes provided include protection for life, travel, personal accident, workmen’s compensation and hospitalisation and surgical requirements.
Sembcorp has championed employee health and well being, both physical and mental, for many years and we promote a holistic and balanced lifestyle for our employees. The Sembcorp Recreation Club, set up in 2005, organises various employee recreation activities including health talks, family days, movie nights and healthy cooking demonstrations, many of which also include employees’ family members. Sembcorp staff have also formed a number of fitness and sports groups which the company supports. In 2009, we spent around S$80,000 on wellness programmes for employees in Singapore.
Sembcorp adopts a practical approach to work-life balance. Examples of initiatives we have put in place include our UK operations’ implementation of flexible working hours, limited working hours (e.g. part-time hours or specific hours to suit family and personal needs) and discretionary leave to support personal situations.
Sembcorp is also a member of the iCare Mental Health Alliance, which, since 2008, has promoted mental health of workers in Singapore. We also offer employees access to counselling and assistance programmes including retirement preparation and workplace accident-related trauma counselling.
In order for contractors to commence work in our facilities, they have to comply with all requirements stated in a ‘Permit to Work’ application, which includes requirements for health and safety provisions. Contractors also have to submit proper paperwork to demonstrate that they have adequate workmen’s compensation insurance coverage for their employees and relevant resident visas and / or work permits. Employees of contractors must also attend HSE training before any work is started. |
|
Sembcorp maintains an ongoing commitment to contribute to the local communities in which we operate through supporting social development and community investment projects.
In 2009, Sembcorp contributed approximately S$1 million in cash and in kind to its communities. Whilst the harsh economic climate may have made giving more difficult for many corporations, we nonetheless took part in many initiatives this year supporting children and education, sports and fitness and community assistance. We also provided management time and support for volunteer programmes.
All contributions are given in Singapore dollars using prevailing exchange rates as at February 22, 2010. |
|
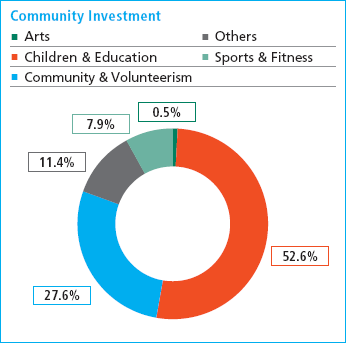 |
|
|
|
|
Of the total amount contributed by Sembcorp, over half was in aid of children and education, which has been a long-standing area of commitment for the Group. This included over S$68,000 to support a social work programme for at-risk youth in Singapore by Wings Counselling Centre.
As part of a three-year commitment, Sembcorp continued to support the Assisi Hospice in 2009 with a contribution of S$66,000. Sembcorp employees also organised a Christmas celebration and dinner for patients, staff and friends of the hospice.
Outside of Singapore, we also contributed actively to the communities we operate in overseas. In 2009, our Industrial Parks business in Vietnam held its annual fundraising event involving tenants, workers, business partners and suppliers. This event raised a total of S$62,000 towards scholarships and the upgrading of schools in Binh Duong province, where our first and second Vietnam Singapore Industrial Park projects are located. Meanwhile, our UK operations contributed around S$111,000 to its local community, including contributions to local schools.
For further information on sustainability at Sembcorp Industries, please visit our website at www.sembcorp.com. If you have any comments or wish to discuss any of the contents of this report or other sustainability issues, please contact:
Group Corporate Relations Tel: +65 6723 3113 Fax: +65 6822 3240 Email: [email protected] |
|
|
|
|
|
|
|
|
|