|
|
|
|
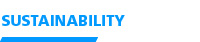 |
|
 |
|
Sembcorp’s priority is to deliver long-term value
and sustainable returns to our shareholders. As a
multinational enterprise and a public listed company,
we understand that there is a complex value chain
to which Sembcorp belongs and that our wider
responsibility incorporates sustainability issues. We
fully recognise that these issues may be outside the
traditional view of corporate activity, but as the
global business landscape evolves, managing these
issues is increasingly viewed as vital in maintaining
a company’s ’licence to operate’ from society and
their stakeholders.
This widening role of business is taken seriously and
is reflected in Sembcorp’s commitment to excellence and
continuous improvement. In our management approach
to sustainability and governance, many issues are directly
addressed at the Group level with the support and
input of the business units. Our management of
material issues of health, safety and environmental (HSE)
performance as well as corporate governance and risk
management and mitigation contributes to enhancing
and preserving the value of our business. In addition,
we continue to maintain an ongoing commitment to
community investment initiatives.
With customers and operations around the world,
Sembcorp is an international company. Our three
main operating units comprise our Utilities business
(which now includes the solid waste management
business), as well as our Marine and Industrial Parks
businesses. As our Marine business is separately listed
in Singapore and reports its activities in a separate
annual report, this report will primarily cover the other
two business units (BUs). Data for key performance
indicators for these BUs has been tracked and reported
in the areas of environment, health and safety, human
resources and community investment. Aside from this chapter, information on the company’s corporate
governance, risk management and mitigation
strategies, and investor relations which are part of the
wider ambit of sustainability issues, may be found in
the relevant chapters under the Environmental, Social &
Governance (ESG) Review section of this annual report.
The following sustainability report addresses the
activities and data that fall within the company’s
financial year for the period from January 1 to
December 31, 2010. Sembcorp has included aspects
of sustainability in our annual report since 2001, and
sustainability issues were last reported in our annual
report for the financial year 2009 published in 2010,
which applied the Global Reporting Initiative (GRI) G3
reporting principles and framework and aspects of the
GRI Electric Utility Sector Supplement on a voluntary
basis. Sembcorp was one of the first companies listed
on the Singapore Stock Exchange (SGX) to publish
a voluntary sustainability report using the GRI G3
guidelines as a reporting framework. This year, we
have continued to use the reporting principles and
framework for the GRI G3 and considered the principles
of the GRI in terms of materiality, stakeholder
inclusiveness, sustainability context, completeness,
accuracy and comparability.
Our aim is to work towards providing readers
with an accurate, complete and reliable report
that contains meaningful information on how we
manage sustainability issues in our specific business
sectors. We have tried to incorporate as much data as
possible from our ongoing operations and the scope
of this report includes reporting on our majority
owned business units, particularly our operations in
Singapore and the UK. This year, we have been able
to include some additional information from our
Utilities operations in China, Vietnam and the UAE.
In 2010, Sembcorp acquired a 97.66% stake in Cascal,
a provider of water services to the municipal market
with operations in China, Indonesia, Philippines, South Africa, the UK, the Caribbean, Chile and Panama.
The data presented in this report excludes our newly
acquired operations under Cascal as well as Shanghai
Cao Jing Co-generation in China where we hold a
minority stake. Where data is unavailable or has
been excluded, this has been clearly stated, and data
measurement is in line with GRI G3 recommendations
for our chosen indicators. Sembcorp is committed to
continuous improvement and aims to expand the scope
of the report in the future. Our target for our ongoing
reporting development is to incorporate reporting on
BUs in which Sembcorp has a majority stake.
Issues that are material to Sembcorp and its
stakeholders are reviewed on an ongoing basis as the
company continues to expand in terms of size and
geography. In general, Sembcorp’s management and
monitoring of sustainability issues is based on a risk
management approach. We have also identified the
AA1000 five-part materiality test as a useful tool to
identify material areas to address and have begun
using feedback obtained through a pilot stakeholder
survey in line with AA1000 to better understand the
Group’s sustainability risk profile.
In addition, we recognise that there are tremendous
opportunities to actively invest in sustainable business
lines. Using our integrated group strength, we apply
proven technologies to produce energy in greener ways,
create innovative solutions for clean, sustainable water
and help manage resources through the treatment and
recovery of recyclables from waste. In this way, we not
only do our part to limit the impact of our activities on
the environment while staying competitive, but also
help our customers to do the same.
At Sembcorp, we recognise the importance of being
an active player within our industry and engaging with our peers and the wider business community on
sustainability issues. Sembcorp is a founding member
and supporter of the Singapore Compact for Corporate
Social Responsibility, a national society promoting
sustainability issues in Singapore.
At the industry level, Sembcorp participates in
the Responsible Care voluntary initiative, endorsed
in Singapore by the Singapore Chemical Industry
Council. This encourages members to adopt 10
guiding principles for a safer chemical industry
through the six management practices of employee
health and safety, distribution, pollution prevention,
process safety, product stewardship and community
awareness and emergency response. In Singapore,
Sembcorp is also a member of the Sakra Island
Community Awareness Group, which seeks to
promote community awareness and a standardised
management practice code for emergency responses
among companies located in the Sakra district on
Singapore’s Jurong Island. Similarly, our Teesside UK
operations are also active in the Northeast England
Process Industry Cluster which serves as a unified voice
for the process industry in northeast England, where
a substantial part of the UK’s chemical, petrochemical,
speciality chemical, pharmaceutical, polymer and
biotechnology industries are based. In the UAE,
our operations in Fujairah participated in the Abu
Dhabi Water and Electricity Authority’s task force in
formulating HSE procedures and guidelines for the
energy sector.
Our internal stakeholders are also crucial in our
day-to-day practice of sustainability and in determining
our sustainability-related risks and identifying areas
for future improvement. As part of our efforts to
create a culture of open, two-way communication,
employees are encouraged to contribute ideas on
improving workplace practices and the delivery of
products and services. This includes feedback on issues
such as dishonesty and fraud via our whistle-blowing
scheme and confidential feedback channels. To
further promote sustainability as a part of Sembcorp’s
corporate culture, employee appraisals take into
account HSE performance.
Sembcorp’s supply chain is a complex one and our
actions influence both our own businesses and others
along the value chains we operate in. Many of our multinational clients are in the process of developing
and integrating their own sustainability programmes
and Sembcorp aims to be a key provider in assisting
them to improve their HSE performance, limit their
environmental impact and conserve resources.
As a provider of utilities, Sembcorp directly
consumes primary resources, produces waste and
emissions and manages and maintains buildings,
people, treatment processes and machinery. As a result,
we must work closely with our suppliers, business
partners and contractors to promote sustainability.
Our commitment to aspects such as HSE performance,
pollution control at source and waste management,
ensures that our policies and practices deliver wider
benefits to relevant stakeholders groups. For example,
Sembcorp assesses general contractor capability to
ensure that projects carried out are in line with our
HSE policy. Through platforms such as contractor HSE committee meetings, safety induction programmes
as well as vendor performance audits, we also
work alongside suppliers to actively identify and
improve performance.
Our company’s main stakeholder groups have
been identified as regulators, financial institutions,
shareholders and the investment community,
suppliers, customers, members of communities where
we have operations as well as our employees. To
better understand our internal and external business
environment, Sembcorp actively engages with
its stakeholders.
Between 2009 and 2010, we carried out a pilot
stakeholder engagement project applying the AA1000
Stakeholder Engagement Standard to seek the views
of stakeholder groups such as investors, customers, suppliers and employees, as well as a Singapore non-governmental
organisations, to better understand
their expectations for Sembcorp’s practice of
sustainability. Questionnaires and telephone interviews
were used to gather data and to ensure neutrality
and openness in the engagement process, external
consultants were appointed to undertake the project
and report on its findings.
The top issues which internal stakeholders felt
were important were health and safety, corporate
governance, labour rights and continued development
of green business lines. A need for training to further
enhance knowledge in the sustainability domain was
also identified. There was also a consensus amongst
external stakeholders that Sembcorp’s reputation for
sustainable practices and sustainability reporting is
important. HSE performance and compliance with
regulatory requirements were high priorities. Suppliers
highlighted the importance of working collaboratively
to anticipate and comply with future regulations,
achieve efficiency in energy and water usage, and
reduce the carbon footprint of our operations.
Investors identified a number of issues important
for companies’ sustainability in general and also
specifically for Sembcorp. These included identification
of material issues, ESG targets and performance in
identified areas, and the use of external guidelines
such as GRI guidelines, amongst others.
Through this and other formal engagement
processes, we aim to continue to align relevant
stakeholder issues with our overall strategy.
In line with our continual drive for innovation
and to widen our sustainable business portfolio, the
development of sustainable or ’green’ business lines
has become a growing part of our ongoing businesses.
We foresee sustainable products and services delivering
an additional competitive edge and enhancing our
reputation as a responsible and responsive company.
Sembcorp’s sustainable business operations include:
Sembcorp runs a 35 megawatt power station that
uses sustainable wood for fuel, the Sembcorp Biomass
Power Station, as a core part of its energy operations
at the Wilton International site in Teesside, UK. The
plant was the first large-scale wood-fired renewable energy plant in the country. To further improve
efficiency of the station, work is underway on a
S$10 million (£5 million) modification to convert
the facility into a combined heat and power facility,
which will make the power station even more
environmentally friendly.
Sembcorp was Singapore’s first commercial importer
and retailer of natural gas, considered the cleanest of
all fossil fuels. We import 341 billion British thermal
units of natural gas per day from West Natuna in
Indonesia and supply major power generation and
petrochemical companies. Starting in late 2011, we
will import an additional 90 billion British thermal
units of gas per day.
Sembcorp aims to apply technology to achieve
greater efficiency and lower emissions in our power,
steam and desalination operations. A summary of
our use of such technologies may be seen in the
table below.
In May 2010, Sembcorp announced a joint venture
agreement with Gayatri Energy Ventures to build,
own and operate a 1,320 megawatt coal-fired power
plant in Krishnapatnam, India. While the plant will
be fired by coal, it will utilise supercritical technology
which reduces emissions of carbon dioxide and other
pollutants by consuming less fuel per unit of electricity
generated, reducing its associated environmental
impacts. Sembcorp expects the power plant to be
70% fuelled by low sulphur non-coking coal sourced
from within India.
Through Sembcorp’s range of services, waste
that would usually be disposed of in landfill and
incineration facilities is diverted for recycling. We also
have capabilities in advanced waste treatment and
resource recovery, including composting and waste-to-energy
recovery. In Australia, Sembcorp’s solid waste
management arm, SITA Environmental Solutions, is a
leader in the development and operation of advanced
resource recovery facilities.
Our waste-to-resource facilities in Singapore
extract recyclables from waste collected through our
municipal waste collection arm, which is the leading
operator in Singapore, serving four out of the nation’s
nine municipal sectors. Sembcorp also operates a
construction and demolition materials recovery facility
in Singapore capable of processing 300,000 tonnes of
construction and demolition waste per year. Timber,
hardcore and fines, as well as ferrous and non-ferrous
metals are recovered during the sorting process.
Furthermore, the complete range of waste paper
recycling services is offered from collection, sorting
and baling to bulk supply of recovered paper to
paper manufacturers. With more than 20 years of
experience in waste paper recycling, we have an
extensive network collecting some 300 tonnes of
waste paper each day.
Sembcorp is a pioneer in industrial wastewater
treatment and water reclamation in Singapore and
China. Our industrial wastewater facilities in China
and Singapore are capable of treating wastewater
up to 20 times more concentrated than municipal
sewage and up to 1.5 times more saline than seawater,
and help to limit the impact of industries on the
environment by treating their effluent to meet
environmental limits.
In 2010, Sembcorp successfully expanded our high concentration industrial wastewater treatment
business with the completion of a second plant in
China capable of treating concentrated industrial
wastewater from source, located at the Nanjing
Chemical Industrial Park. The new facility is capable
of treating up to 12,500 cubic metres of effluent per
day without customers having to pre-treat it first. This
saves customers the need to invest in pre-treatment
facilities for their wastewater, and at the same
time, also supports local authorities in their goal of
environmental protection. Meanwhile, in Singapore,
we announced the upcoming development of a new
integrated wastewater treatment plant to serve
growing customer needs in the newly developed area
of the Jurong Island petrochemical manufacturing
cluster. Capable of treating multiple streams of
complex industrial wastewater, the plant will more
than double the current industrial wastewater
treatment capacity on Jurong Island with its initial
capacity of 9,600 cubic metres per day.
Beyond treating wastewater, Sembcorp also reclaims
water from treated effluent, conserving precious
water resources and offering a sustainably-sourced
alternative water supply to industries and households.
In Singapore, the company was the first company to
reclaim secondary effluents from wastewater, applying
dual-media filtration, microfiltration, reverse osmosis
and ion exchange technologies to produce high purity
demineralised water and high grade industrial water for supply to its customers. Today, Sembcorp’s supply
of demineralised water and high grade industrial
water to customers in Singapore is substantially
derived from reclaimed water. Our ability to integrate
wastewater treatment, water reclamation and water
supply in a ’closed loop’ minimises liquid discharge,
conserves potable water supplies and promotes a
sustainable water supply.
In 2010, Sembcorp officially opened its Sembcorp
NEWater plant, one of the largest water recycling
plants in the world, with a capacity of 228,000 cubic
metres per day. The plant’s completion marked a
major step in Singapore’s water sustainability journey.
It is one of the few water reuse plants in the world
to be built on top of another water reclamation
treatment plant, minimising its plant footprint in
a land-scarce country. The facility’s state-of-the-art
microfiltration and reverse osmosis systems are also
designed for optimum energy consumption.
Sembcorp’s Industrial Parks business applies an
integrated approach to township development,
providing world-class manufacturing space coupled with
an environmentally sensitive approach to development.
In January 2010, we held a groundbreaking
ceremony for our fourth Vietnam Singapore
Industrial Park (VSIP) development in Hai Phong,
Vietnam. Integrating conservation considerations in
its masterplan, 30% of land within the development
is reserved for green space and the preservation of
local flora and fauna. Existing wetlands on the site
as well as tributaries from the Cam River that run
through the township will be preserved and made a
feature of the development. Vietnam, with its growing
trend of urban migration, requires sustainable urban
solutions. With its environmentally sensitive approach
to development, VSIP Hai Phong has potential to be
a showcase of such sustainable urban development in
the country.
In 2010, we also completed the conceptual
masterplan for the 1,500 hectare Sino-Singapore
Nanjing Eco High-tech Island (SNEI) in China’s Jiangsu
province. Leveraging on the central government’s
long term goal of creating a sustainable economy
with environmental preservation, 870 hectares of
the SNEI’s gross land area will be preserved for eco-tourism.
The remaining 630 hectare development
area will feature eco-friendly residential designs
and knowledge industry development. The SNEI is
envisioned to render the Jiangxinzhou island on
which it resides as a model for sustainable growth
characterised by eco-styled urbanisation.
Research and development plays an important
role in strengthening Sembcorp’s sustainable
capabilities. As a business, our continued drive for
technology and innovation allows us to optimise
existing facilities and processes and use energy
more efficiently. This means better use of resources,
lower costs, better safety performance and reduced
environmental impact.
Sembcorp’s operations are supported by our in-house
Technology department, as well as the collective
expertise of our entire Group. In addition, in 2010,
we also set up a Group Technology Committee that is
headed by Sembcorp’s Chairman and Group President
& CEO. We also form research arrangements and
collaborations with local tertiary research institutes
and water technology companies. An example of
such a partnership is our ongoing collaboration
with Nanyang Technological University’s Nanyang
Environment and Water Research Institute, to jointly
explore new technology to remove recalcitrant organic
materials from complex industrial wastewater. Pulling
together these extensive intellectual resources, our
continued push for technology and innovation helps
to build our competitive advantage and support the
sustainable growth of the Group.
In 2010, Sembcorp received both national and
global recognition and a number of awards for its
efforts to promote and practise sustainability.
The Sembcorp NEWater Plant was recognised
for its contribution to the international water reuse
industry, winning the 2010 Global Water Awards Water
Reuse Project of the Year, as well as the WateReuse
Association’s WateReuse International Award. One of
the largest water reuse plants in the world, the plant
uses state-of-the-art technology to optimise land
use, has a compact plant footprint and strengthens
Singapore’s supply of NEWater, an ultra-clean, high-grade
reclaimed water which is a key pillar of the
country’s water sustainability strategy.
Sembcorp received Responsible Care Achievement
Awards from the Singapore Chemical Industry Council
in 2010 for Responsible Care’s Employee Health &
Safety, Pollution Prevention and Process Safety codes.
The awards honour companies which incorporate
Responsible Care Management Practices in their
operations, and maintain high health, safety and
environmental standards.
Sembcorp was ranked Singapore’s Most Transparent
Company in the multi-industry / conglomerates
category at the Securities Investors Association
(Singapore) Investors’ Choice Awards. The awards
recognise companies that adopt good corporate
governance practices through their efforts towards
excellent financial reporting and extensive disclosure
of information.
The bizSAFE programme, initiated by the Workplace
Safety and Health Council in Singapore, promotes
workplace safety and health through recognition
of companies’ safety efforts. Sembcorp Cogen and
Sembcorp’s Singapore solid waste management unit
achieved the highest level, or ’star’ status in 2010.
Sembcorp won three silver awards at the Singapore
Workplace Safety and Health Performance Awards
2010. The annual awards are presented to organisations
that have performed well by implementing sound
health and safety management systems. The three silver
awards were received by Sembcorp Gas, Sembcorp
Cogen and our propylene purification operations.
Sembcorp’s solid waste management subsidiary
SembWaste clinched Singapore’s top Total Defence
Award, the Minister for Defence Award, for its
outstanding contributions to total defence, especially
for its medical waste collection services during the
outbreak of Influenza A (H1N1) in Singapore in 2009.
The UK Water Services Regulation Authority (Ofwat)
ranked Sembcorp’s municipal water operations in
Bournemouth in UK, as the joint top performing water
company for service delivery in England and Wales,
maintaining the unit’s number one ranking for the
second year in a row. The company achieved its best
ever performance by scoring 288 points, the maximum
possible in the regulator’s assessment of the overall
quality of service, including reliability and continuity of
water supply, drinking water quality, and management
of leakage provided by water companies.
Sembcorp’s operations in Teesside in UK were
honoured twice at the prestigious UK National Training
Awards 2010. The vastly experienced Protection
Team won both a Regional and National Training
Award in recognition of Sembcorp’s outstanding
contribution and commitment to training, learning
and development in the workplace. Sembcorp was
the first in UK to put its entire industrial fire-fighting
force of almost 100 site protection officers through a
new Level 3 National Vocational Qualification designed
specifically for professionals in the fire-fighting and
rescue sector.
In 2010, Sembcorp’s VSIP was presented a Saigon
Times Top 40 Award by The Saigon Times and the local Department of Planning and Investment. This prestigious
award recognised the best performing foreign direct
investment enterprises and their efforts towards
environmental conservation and sustainability, as well as
their contributions to the economy and community.
VSIP’s efforts have been endorsed by the Vietnam
Association for Conservation of Nature and Environment,
who awarded VSIP with its Greentech Certificate
in recognition of its proactive efforts in managing
environmental issues and implementing measures for
environmental sustainability.
Our operations in Mbombela, South Africa, were
amongst the only 5% of the country’s water networks
to be given ’Blue Drop’ status by the Department of
Environment and Water Affairs, in recognition of
their provision of high quality water services. The Blue
Drop scheme is meant to build public confidence in
the quality of the drinking water and to ensure that
proper monitoring measures are taken to ensure safe
drinking water.
HSE issues are clearly linked with Sembcorp’s long-term
success, and have been identified as material
factors in terms of their potential impact on our
business operations, as reflected in feedback from
our stakeholder engagement survey. Expectations of
our key stakeholder groups continue to increase in
this area and our HSE performance is an important
component of assessment for the Group as a high
quality investment, business partner and supplier.
The Group HSE policy can be viewed on our website at
www.sembcorp.com. In managing our HSE issues, we
continue to be guided by four main principles:
• |
Implementing internationally recognised HSE
management systems such as ISO 14001:2004
and OSHAS18001:2007. |
• |
Actively investing in financially viable sustainable
business lines, which form part of our core operations. |
• |
Pursuing continuous improvement to enhance HSE
performance of our processes, products and services. |
• |
Working closely with our business partners and seeking active engagement to promote mutual HSE performance improvement and positive impacts. |
This section of the report provides information
on how the Group proactively manages HSE impacts
arising from its operations. It covers key issues
including clean air and climate change, water, waste
and the health and safety of our employees and
business partners.
This 2010 report includes data from not only
Singapore and the UK, which were the main focus
of the 2009 report, but also from operations in
Vietnam, the UAE and China (excluding newly acquired
operations from Cascal as well as Shanghai Cao Jing
Co-generation where we hold a minority stake). In the
case of some indicators, this broader scope of reporting
may mean that there is no meaningful comparable
year-on-year data.
With operations that spread across six continents,
our Group HSE department is the driver of our
management systems and co-ordinates our global
HSE efforts. Management committees and reporting
structures have been established with regional
co-ordinators working closely with the Group HSE
department. This ensures the effective management
of HSE issues with the purpose of setting long-term
HSE objectives and targets and complying with the
regulatory requirements, voluntary group guidelines,
standards and initiatives. From early 2011, HSE issues
have been incorporated into regular reports to the
board and key HSE risks and controls have also been
presented to the board’s Risk Committee.
In 2010, Sembcorp’s growth presented the challenge
of aligning HSE policies and standards throughout
the company, particularly in our newer operating
sites. Going forward, our priority continues to be on
aligning and improving standards across the Group and
proactively managing HSE throughout the entire asset
management life cycle, from business development
and project conception, through to operation until
end of the life of the asset.
The HSE culture at Sembcorp is one of shared
responsibility, involving everyone associated with the
company. With this approach, employees, business
partners and contractors take ownership of day-to-day
health, safety and environmental performance,
and meet expected standards. We continue to work
with our partners and suppliers towards mutual HSE
improvement. In Singapore, the Sembcorp Contractor
HSE Committee continues to promote co-operation
with our contractors in achieving and maintaining
HSE performance on Jurong Island.
As a key player in the energy sector, we are keenly
aware of global climate change issues. We aim to
limit and manage the impact of our operations on
climate change by enhancing our efficiency and
investing in assets applying technologies which manage
and reduce emissions.
Data shown in this section is from operations in
Singapore and Teesside in the UK unless otherwise stated.
Compilation of our emissions data is in accordance to the
World Resource Institute and World Business Council for
Sustainable Development’s Greenhouse Gas Protocol for
Stationary Combustion (Version 4).
In our Singapore and Teesside UK operations,
carbon dioxide emissions have remained at around
the same levels as in 2009 at around 2,330 kilotonnes
and 790 kilotonnes respectively.
In addition to carbon dioxide emissions, we have
begun to widen the scope of our data to include
other sources of emissions.
In 2009, due to a natural gas curtailment by our
suppliers, our Singapore operations substituted natural
gas with fuel oil and emitted 85 tonnes of oxides of
sulphur (SOx). SOx emissions have since decreased
by more than 60% to 30 tonnes in 2010. In Teesside,
UK, SOx emissions were also reduced by more than
40%, from 978 tonnes in 2009 to 564 tonnes in 2010.
Total emissions of oxides of nitrogen (NOx) for our
operations in Singapore and Teesside in UK in 2010
decreased by more than 50% as compared to 2009.
In Singapore, NOx emissions decreased by more than
70%, from 1,707 tonnes in 2009 to 461 tonnes in 2010
due to lower utilisation of boilers as a result of an
increase in the export of steam by our cogeneration
plant. In Teesside, UK, NOx emissions also reduced by
more than 20%, from 1,135 tonnes in 2009 to 859 tonnes in 2010. Reduction in SOx and NOx emissions
from operations in Teesside in the UK was due to the
lower utilisation of coal boilers during the year.
We continued to track our primary energy sources
usage in 2010. Natural gas continued to account
for the largest proportion of our fuels used. We also
continued to monitor indirect energy usage in the
form of electricity consumption by our operations within the scope of the report; this was over 2.3 million
gigajoules for 2010.
Our water business has grown significantly over
the last five years through acquisitions and organic
growth. We provide a range of services from
specialised industrial wastewater treatment to water
reclamation, desalination and the supply of potable
and industrial water. Sembcorp manages facilities
capable of producing and treating over six million
cubic metres of water and wastewater daily and
serves close to five million people worldwide. Through
innovation, we make every effort to ensure the
efficient use and reuse of water resources.
As part of our water solutions to our customers,
we treat and supply water extracted from surface
water and groundwater (including lakes, rivers,
oceans and aquifers). In 2010 for our operations in
Singapore, Teesside in UK, China (excluding newly
acquired operations from Cascal as well as Shanghai
Cao Jing Co-generation), Vietnam and the UAE, we
extracted 815 million cubic metres of surface water
and groundwater, primarily for treatment and supply
to our customers and for use in our operations.
In 2010, our Teesside operations consumed over
16 million cubic metres of potable and raw water, including raw water consumption used to produce
demineralised water for our customers and for use
in our operations. Sembcorp also recycled 18 million
cubic metres of water for supply to our customers
and for use in our operations in Singapore and
Teesside in UK, reducing the need to draw on
potable or raw water supplies and also helping
our customers to reduce the amount of raw water
needed for their operations.
As one of the largest solid waste management
players in Singapore, Sembcorp provides services
that aim to reduce waste going to incineration or
landfill facilities. We also promote waste reduction
by encouraging recycling. In line with our business
focus to reduce waste for disposal, we are actively
developing differentiating know-how including
waste-to-resource capabilities.
In previous years we have reported on Sembcorp’s
internal SCU 5/0 campaign, which tracks the five goals
of zero injury, zero spill, zero non-compliance, zero
hazardous release and zero unplanned shutdown
and imputes a monetary cost to lapses (termed the
’price of non-conformance’) which is monitored over
time. This internal campaign was initially started
in Singapore for our Utilities operations and has
contributed to a substantial improvement in our
performance since its inception. As part of our efforts
to improve HSE performance across the Group we are
currently reviewing this to see how we can formulate
an enhanced standardised set of HSE reporting
parameters for application across all business units
both in Singapore and overseas.
For 2010 we have been able to extend the scope of
our accident and injury rate reporting. Using indicators
of accident frequency rate (AFR) and accident
severity rate (ASR), in accordance with the tracking
criteria set by Singapore’s Ministry of Manpower, the
safety performance from our Utilities operations in
Singapore, UK, China and the UAE has been recorded
(China operations recorded data from February to
December 2010 only). In 2010 for the first time, we
have included data from our operations in China
(excluding newly acquired operations from Cascal as
well as Shanghai Cao Jing Co-generation) and the UAE. The solid waste management business’ safety
performance in Singapore is reported separately
from the performance of the rest of our Utilities
operations. This is due to the fact that the solid waste
management business’ waste collection operations
employ manual labour to a greater degree and
therefore have a different risk profile from our energy,
water and on-site logistics operations.
Our Utilities operations excluding solid waste
management reported four accidents in 2010 – three
in the UK, including a case involving a contractor,
and one in China, with zero reportable accidents
in Singapore and the UAE. Our Utilities operations
reported 121 man-days lost in 2010, a substantial
improvement compared to 194 days in 2009.
For our solid waste management business in
Singapore, we saw an increase in the AFR from 4.4 in
2009 to 6.4 in 2010. Its ASR also increased from 92.6 in
2009 to 346.9 in 2010. The increase in its accident rates
was mainly due to two accidents which accounted for
more than 50% of the lost work days, with one case
involving an employee breaking his wrist while the
other saw the employee concerned hurting his back in
the course of work.
Safety remains important to us and our solid waste
management business has taken preventative action to
improve its AFR and ASR levels. This includes additional
’toolbox meetings’ with management and employees
to cover the importance of health and safety and spot
inspections at operational sites.
Sembcorp’s solid waste management business
operates a fleet of 170 commercial vehicles and
undertakes a considerable amount of driving each
year. One of our key indicators for this business for
safety is vehicle accidents. In 2010, there was a rise
in the accident rate both in terms of absolute numbers
and number of incidents per 100,000 kilometres driven.
The company has commenced a programme of safety
training for its drivers starting January 2011, and
will continue to track and aim to reduce its vehicle
accident rate.
In 2009, we embarked on an initiative to pull
together our different facilities and operations on
Jurong Island for an integrated ISO14001
Environmental Management System (EMS) certification,
as an effort to align the HSE management certifications.
Backed by strong support from senior management,
we successfully underwent an independent audit and
achieved certification in May 2010. Moving forward,
we have committed to an improvement target to
obtain an integrated certification of the OHSAS18001
Occupational Safety and Health Management System
and the ISO14001 EMS certification for our Singapore
Utilities operations by 2011.
In Singapore, our solid waste management business
under our Utilities business unit received the Flu
Pandemic Preparedness Verification Certificate which
is part of the Singapore Business Federation’s National
Business Continuity Management Programme launched
in 2010.
From 2009 to the end of 2010, we worked to
strengthen our HSE standards at our operations in
Fujairah, UAE. We formalised and enhanced the HSE
management system on the site and completed a
written submission to the local authorities documenting
this enhanced system. Going forward, we aim to work
towards full implementation of the management
system, and to obtain certification to ISO14001 EMS
and OHSAS18001.
In 2010, Sembcorp’s VSIP also obtained the
ISO14001 EMS certification for its environmental
efforts. It is the first industrial park in Vietnam to
receive this certification awarded by Société Générale
de Surveillance (SGS), a leading inspection, verification,
testing and certification company recognised as the
global benchmark for quality and integrity.
Updating our standards and seeking continuous
improvement is part of our Group HSE department’s
mandate. In 2010, a Group HSE workshop was held
where employees from our operations around the
world contributed ideas towards the formulation of
key HSE initiatives as well as a set of global mandatory
HSE guidelines for all business units under our
operational control.
The HSE performance of each business unit was
also presented at the Annual Asset Management and
HSE Workshop in September 2010. HSE incident data
including statistics on injuries, AFR and ASR, spills, non-compliance,
hazardous releases, waste and disposal
and emissions were reported. Significant achievements
and areas for enhancements were also shared for
learning amongst the business units.
In 2010, our Group HSE department continued
with its programme to monitor, review and audit
each business unit’s HSE management system and
performance. In January 2010, a five-day internal
audit for our operations in Fujairah was conducted. The results of this audit were fed into the unit’s
efforts to implement improvements for alignment
to the new UAE Code of Practice, a framework
for the HSE management system. HSE reviews
were also conducted during the year at our water
operations in Nanjing and Zhangjiagang to assess the
implementation of HSE management systems at the
two China sites. Detailed findings and corrective and
improvement actions were presented in a report to
facilitate improvement.
In 2010, the Group HSE office was involved in site
inspections, HSE workshops and events conducted by
the business units as well as training and workshops to
improve HSE performance and manage health, safety
and environment risks associated with our activities,
products and services.
In 2010, training courses on HSE, asset management
and operations and maintenance were held for selected
employees from our China operations, with tailored training materials and presentations conducted
in Mandarin. Similar training was also conducted
for selected employees from Indonesia. The Group
HSE team also conducted a half-day HSE breakout
session during the Group Asset Management and HSE
workshop held for officers from our global operations
in Singapore. This annual event encourages HSE
representatives to network, share best practices, and
contribute to improving our HSE programmes. Ideas
and suggestions contributed by the participants were
collated and considered for incorporation into the
annual Group HSE work plan.
Sembcorp is a signatory of Responsible Care in
Singapore. This is a voluntary initiative of the global
chemical industry for environmental protection,
occupational health and safety, process safety, product
stewardship, distribution, community awareness and
emergency response. In 2010, the Singapore Chemical
Industry Council invited Sembcorp to present on
Responsible Care’s Emergency Response code at its
Responsible Care Good Practices Workshop in August,
where industry players shared good practices with respect
to Responsible Care’s Code of Management Practices.
At Sembcorp, we recognise that our employees
are our most vital assets and a key stakeholder group.
We remain committed to providing a fair, diverse
and inclusive workplace, and to continuous
improvement in our human resource and people
development practices.
This section of the report covers the activities of
Sembcorp Industries’ head office, the Utilities business
unit (which now includes the solid waste management
business), as well as the Industrial Parks, Design
and Construction and Mint business units. We have
expanded data coverage to include operations in all
countries we operate in. Any deviation from this scope
is noted under the individual indicator.
Sembcorp strives to maintain a fair, diverse and
inclusive workplace for all employees. With its headquarters based in Singapore, the Group subscribes
to The Principles of Fair Employment formulated by
the Singapore Tripartite Alliance for Fair Employment
Practices, and has endorsed the Tripartite Alliance’s
Employers’ Pledge of Fair Employment Practices.
These principles, embedded into our human resource
practices and implemented by Sembcorp on a global
level, include a commitment to:
• |
Recruit and select based on merit, such as skills, experience and ability, regardless of age, race, gender, religion or family status. |
• |
Treat employees fairly and with respect and implement progressive human resource management systems. |
• |
Provide equal opportunities for training and development based on employees’ strengths and needs, to help them achieve their full potential. |
• |
Reward fairly based on ability, performance, contribution and experience. |
• |
Abide by labour laws and adopt tripartite guidelines which promote fair employment practices. |
Permanent headcount increased in 2010 with the
acquisition of Cascal and its international municipal
water business. At the end of December 2010, there were about 9,100 permanent employees in the
Sembcorp Group. The Group had a further 5,900
employees working on a contract basis, 80% of whom
work for the Marine business. Please see charts below
for the distribution of Sembcorp’s permanent employees
by geographical region, gender and education.
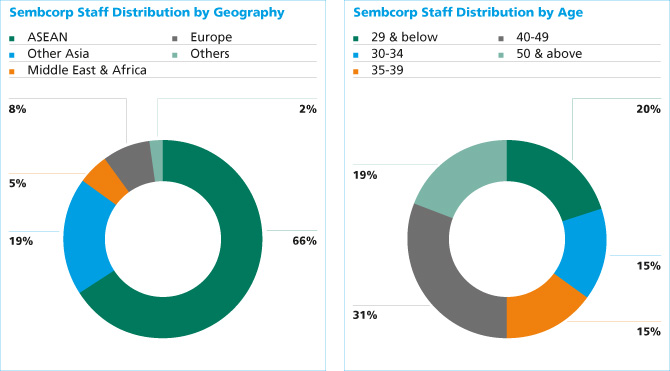 |
|
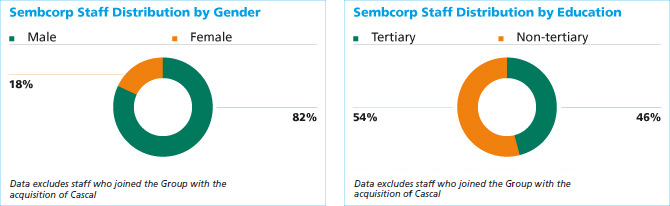 |
Sembcorp fully supports basic principles of
human rights and has implemented a number of
policies throughout the Group in support of these
principles, including fair employment practices and
a grievance and harassment policy. We also offer
equal opportunities with respect to recruitment
and selection.
A key tenet of Sembcorp’s business ethics is strict
respect for labour laws within each of the countries
we operate in. Through our policies and the planning
and administration of our employment practices, we
are confident that our operations are not exposed to
issues such as child or forced labour.
Within the boundaries of each of the legal and regulatory jurisdictions under which we operate, every
Sembcorp employee is entitled to practise freedom
of association in the workplace. At the end of 2010,
there were over 3,000 unionised members in Sembcorp
(including workers under the Marine business),
covering over 30% of our total workforce.
Sembcorp maintains constructive ongoing
exchanges with employee unions in its various
locations. For instance, in the UK, discussions with
Unite, the UK’s biggest union, are conducted in
line with our collective agreement, the ’Together
Agreement’ which covers over 90% of employees at
our Teesside operations. Also in the UK, our municipal
water operations, Sembcorp Bournemouth Water,
has had a long-standing positive relationship with its
recognised unions, GMB and Unison. Both unions are
represented on the unit’s Staff Consultative Group and
Health and Safety Committee, and also participate in
safety inspections. In Singapore, Sembcorp’s various
business units hold regular meetings with the two main
unions, the Union of Power and Gas Employees, as
well as the Building Construction and Timber Industries
Employees’ Union (BATU) to discuss various issues
to help our employees stay competitive. Collective
discussions in 2010 involved annual increments,
variable bonuses and worker skills in specific sectors.
Sembcorp recognises the importance of engaging our
employees. We operate a number of channels through
which we communicate with and receive feedback from
our employees. We provide information on our financial
and business performance, as well as on applicable
company standards and policies to our staff. Interactive staff communications sessions with management are in
place to ensure two-way communication between the
company and its employees.
In 2010, we continued to hold employee briefing
sessions in conjunction with the company’s quarterly
financial reporting cycle. At these sessions, held in
an interactive setting, senior management provides
employees with a first-hand account of the company’s
performance and key developments for the quarter.
In addition, we continued to hold an annual
communication forum in Singapore for managers from
Sembcorp offices all over the world, with in-depth
briefings from top management and invited experts
on our Group’s operating environment, performance,
outlook and strategy. This forum incorporates an
interactive networking and question-and-answer session.
Furthermore, at the country level, some business units
also held quarterly learning and sharing sessions, senior
manager briefings, and staff consultation group sessions.
Over the course of the year, we continued to
communicate corporate updates and business milestones
to all staff through employee email blasts and our
employee e-newsletters. Relevant and up-to-date
information on staff welfare and benefits was also
publicised to employees via the company intranet.
Sembcorp welcomes feedback from its employees
and provides confidential channels through which
employees can submit feedback and staff suggestions,
including an easily-accessible online form on the
employee intranet. All feedback is sent to the Group
Human Resource department, and is also automatically
copied to the Director for Group Human Resource and
to the Group President & CEO’s office if sent via the
staff intranet.
In line with our commitment to high ethical
standards and good corporate governance practices,
we operate a group-wide whistle-blowing policy
and encourage all employees to report any possible
perceived improprieties on a confidential basis and
without fear of recrimination. We have an easily-accessible
whistle-blowing link on our company
intranet, and employees may also provide whistle-blowing
feedback via channels including mail,
email and fax.
Sembcorp continues to promote a holistic and
balanced lifestyle for our employees, which we
believe is good for both their physical and mental
health. We encourage employees at our various business
units to participate in employee recreation events throughout the year, including community outreach
and volunteering events, team sports events, talks,
gatherings and employee family days. We also opened
up some of these activities to include employees’ family
members, such as our Family Day for employees from
Singapore operations. In 2010, we spent over S$100,000
on wellness programmes for employees in Singapore.
In Singapore, we are also part of the iCare Mental
Health Alliance, which seeks to promote workplace
mental health and offers employees access to
counselling and assistance programmes, including
retirement preparation and workplace accident-related
trauma counselling.
Our shared success at Sembcorp is driven by
the calibre and performance of our people. We recognise that it is essential to equip our employees across all
levels of seniority to meet the changing needs of the
marketplace. Sembcorp offers employees a range of
personal and professional development opportunities
including career development, education, talent
management and leadership programmes.
In 2010, the Group continued to invest in
competency building for our employees, spending
S$1.6 million on training for employees in Singapore
alone. It is a priority for us to enhance the skills
levels of our employees to ensure smooth succession.
Sembcorp’s learning and development programmes
factor in issues such as succession planning and
addressing skills gaps with relation to core competency
requirements. About 1.7% of our employees in
Singapore are due for retirement in the next five years.
Our training and development programmes include:
• |
The ’Sembcorp Leadership Competencies’ is
our unique talent management and development
system that defines the qualities and performance
expectations of a Sembcorp leader. Capable leaders
are a crucial component in achieving extraordinary
business success and this set of competencies details
the ways in which Sembcorp leaders should act and
respond. Managers also attend courses to enhance
their presentation, negotiation, communication and
coaching skills, as well as courses on building and
leading high-performance teams.
Senior executives are expected to undertake
regular training to update and upgrade their skills,
and education programmes are accessible for them at
prestigious institutes such as the Harvard Business School,
INSEAD and the Temasek Business Leadership Centre. |
• |
At Sembcorp, we offer employees experience in
different cultural and operational settings through job
rotations and attachments. For instance, we currently
have more than 50 employees of different nationalities
posted from our Singapore office to various overseas
businesses. Internships and industrial attachments also
provide students and Sembcorp scholars with practical
experience and exposure to our operations whilst they
undergo their studies.
Overseas site visits are also useful in offering
employees exposure and in promoting the sharing of
expertise across Sembcorp’s international operations.
For instance, in 2010 we held a series of working tours
and development visits for China-based employees at
our facilities on Jurong Island, Singapore. |
• |
At Sembcorp, we send our employees for professional
training to allow them to develop skill sets to equip
them to better perform their jobs.
Working with local educational institutions,
Sembcorp has developed and conducted specialised
technical courses for the Utilities business, including
a certified energy manager course by the Institute of
Engineers in Singapore and a basic boiler and cooling
water treatment course by Nalco, a leading process
improvement company serving the industrial water
and energy industries. Sembcorp also sends many
of our employees for professional training related
to the industry, including courses under Singapore’s
National Skills Recognition Scheme and Workforce
Skills Qualification scheme under the Workforce
Development Authority.
Overseas, our employees also continued to receive
training. For example, selected employees at our
operations in Mbombela, South Africa, underwent
Adult Basic Education and Training to equip them with
foundation skills in areas such as English, mathematical
and computer literacy.
In addition, we also run on-the-job training for
our employees. |
• |
As an industry leader in various sectors, Sembcorp
encourages our employees to share and exchange
best practices through platforms such as seminars and
conferences on a local and international basis. |
Sembcorp has implemented a standard system for
performance appraisals across our operations in various
countries. The appraisal system allows employees to
comment on their personal contribution throughout
the year and to jointly identify areas for further career
development and learning with their supervisors. It
enables constructive discussion and uses the feedback
process to ensure that employees share the responsibility
for managing their career and goals. The appraisal
process incorporates shared future objectives to ensure
that employee outputs are also aligned to the needs of
the business.
Selected senior managers are also assessed using a
360-degree appraisal system where feedback is sought
from a range of superiors, peers and colleagues and
other partners. The profile of essential competencies
for the job function compiled from this process is also
incorporated into these managers’ development plans,
helping them to lead their teams successfully and
enhance their professional performance.
Rewarding performance is a cornerstone of
Sembcorp’s employee retention strategy. The Group
offers competitive base pay packages throughout our
global businesses that are based on country-specific
conditions. Rewards include annual salary increments
and annual performance bonuses, as well as longer-term
incentives linked to sector practices and based
on the performance of the Group, the company and
the individual.
Share-based incentives, administered by a board-nominated committee, remain a key component
of the Group’s pay structure and are deliberately
aligned to long-term Group performance objectives.
Since 2007, share options granted to staff have been
replaced with restricted stocks of equivalent fair value.
This Restricted Share Plan applies to employees of the
Group, while the Performance Share Plan is aimed
primarily at key executives of the Group.
All employees are eligible for comprehensive
insurance coverage on a global basis. They can join
the company’s private medical insurance scheme,
under which the company meets the cost of employee
membership and allows employees to include eligible
dependants. The company also provides additional
insurance cover for life, travel, personal accidents,
workers’ compensation and hospitalisation and
surgical requirements.
In Singapore, where 86% of Sembcorp’s contract
workers are employed, we require contractors to
comply with all requirements stated in a Permit to
Work application issued by the Ministry of Manpower,
before they can work in our facilities or operating
sites. This includes requirements for health and safety
provisions and the submission of proper paperwork
to demonstrate the presence of adequate workers’
compensation insurance coverage, as well as relevant
resident visa and work permits. Employees of our
contractors must also attend health, safety and
environment training before any work is started.
As an active corporate citizen, Sembcorp
maintains an ongoing commitment to contribute to
the local communities in which we operate through
supporting social development and community
investment projects. In 2010, Sembcorp contributed
over S$1 million in cash and in kind to its communities,
excluding community investment initiatives by our
separately-listed Marine business. We took part
in many initiatives in our communities in support
of children and the elderly, education, sports and
fitness and the environment, amongst others. We
also provided management time and support for
volunteer programmes.
Our employees actively participate in volunteerism
initiatives that the company organises. For example, in Singapore, our employees participated in fundraising
activities organised by the Assisi Hospice and volunteered to help clean the homes of the needy
elderly under the care of Sunshine Welfare Action
Mission. In Singapore, our employees spent more than
1,800 hours on volunteerism in 2010. Our employees
overseas also participated in volunteerism initiatives.
For instance, employees from our operations in
Bournemouth in the UK support and promote the
work of international water charity, WaterAid, through
giving presentations to schools, groups and clubs in
their local area on WaterAid’s work.
Sembcorp supports projects that help to support
outreach activities to the communities. For instance,
in Singapore, Sembcorp supported the National Parks
Board’s initiative to enhance and promote appreciation
of biodiversity through the launch of the Sembcorp
Forest of Giants.
During the year, Sembcorp also continued to
contribute to programmes in aid of sports and in
support of young sportsmen pursuing their dreams. In
Singapore, we sponsored S$50,000 worth of scholarships
and bursaries for promising young badminton players
through an ongoing programme jointly administered by the company and the Singapore Badminton Association.
In addition, we also pledged S$300,000 over three years
to the Singapore Table Tennis Association towards
support of the national table tennis team as well as
the association’s efforts to raise the level of the game
locally and help to nurture more table tennis talents.
Siza Water, our operations in South Africa, administers
a Youth and Community Development Fund which
sponsors schools with sports equipment and gear to
support students at sports games.
We have taken part in many initiatives supporting
children and education. For instance our operations in
Teesside in the UK helped organise educational visits to
our facilities at Sembcorp’s Wilton International,
a chemical manufacturing site at Teesside.
Sembcorp also contributed to programmes
supporting wildlife and biodiversity. For instance,
Sembcorp municipal water operations in Bournemouth,
UK continued to maintain its long-standing support of
Dorset Wildlife Trust, which has more than 40 nature
reserves covering 1,300 hectares of wildlife habitat
and five education centres in the local area. In addition,
during the year the unit donated one of its former
vans to local volunteer wildlife aid group Dorset
Wildlife Rescue (DWR) to be used as an ambulance
for transporting injured, sick or orphaned wild
mammals and birds of prey across Dorset, Hampshire
and Wiltshire.
For further information on sustainability at Sembcorp Industries, please visit our website at www.sembcorp.com. If you have any comments or wish to discuss any of the contents of this report or other sustainability issues, please contact:
Group Corporate Relations
Tel: +65 6723 3113
Email: [email protected] |
|
|
|
|
|