|
|
|
|
 |
|
 |
|
Sembcorp’s priority is to deliver long-term value
and sustainable returns to its shareholders. As a
multinational enterprise and a public listed company,
we understand that there is a complex value chain
to which Sembcorp belongs and that our wider
responsibility incorporates sustainability issues. We
recognise that these issues may be outside the
traditional view of corporate activity, but as the global
business landscape evolves, managing these issues is
increasingly viewed as vital in maintaining a company’s
‘licence to operate’ by society and our stakeholders.
This widening role of business is taken seriously
and is reflected in Sembcorp’s commitment to
excellence and continuous improvement. In late 2011,
we established a Sustainability Steering Committee
to drive Sembcorp’s sustainability performance and
to develop our priorities across the Group. The
Committee will also review our sustainability roadmap
and make strategic recommendations to improve
sustainability performance across the organisation.
The Committee is chaired by the Chief Health, Safety
and Environment Officer and Executive Vice President
of Group Asset Management.
Sembcorp’s management and monitoring of
sustainability issues is based on a risk management
approach. Issues that are material to Sembcorp and
our stakeholders are reviewed on an ongoing basis as
the company continues to expand. In late 2011, a
materiality review was conducted by an independent
consultant to identify the company’s key sustainability
issues. This involved identifying potential issues
and prioritising them based on a Materiality Matrix
approach, which charts their level of importance
to Sembcorp and our stakeholders, using clearly
defined materiality criteria. The initial findings of the
review identified key sustainability issues such as
environmental protection and safety. We will be
taking steps to engage our key stakeholders on the
findings of this initial review.
Sembcorp is an international company with
customers and operations around the world. In 2011,
we focused on enhancing our sustainability data
management systems and as a result, we have been
able to broaden the scope of our sustainability
reporting this year. The data in this year’s report
covers all our Utilities business units where Sembcorp
has either operational control or majority ownership
in Singapore, China, the UAE, UK and Vietnam. We
have also been able to include data from our China
and UK municipal water operations which we
acquired in 2010.
Our Marine business is excluded from this report,
as it is separately listed in Singapore and reports its
activities separately. Our target for our ongoing
reporting is to incorporate data from all businesses
in which Sembcorp has a majority stake or
operational control.
Data and activities for key performance indicators
for the included operations have been tracked and
reported in the areas of:
|
|
• |
Health, safety and environment |
• |
Human resource and employee welfare |
• |
Wider community |
|
|
Where data is unavailable or has been excluded,
this has been clearly stated. All data measurement
is in line with Global Reporting Initiative (GRI) G3.1
recommendations for our chosen indicators.
Further information on the company’s corporate
governance, risk management & mitigation strategies
and investor relations, all of which are part of our
wider remit of sustainability, can be found in the
relevant chapters under the Environmental, Social &
Governance Review section of this annual report.
Sembcorp has included aspects of sustainability
in our annual report since 2001 and was one of
the first companies listed on the Singapore
Stock Exchange to publish a voluntary sustainability
report using the GRI G3 guidelines. We continue
to use the reporting principles and framework
of GRI and have considered its principles in
terms of materiality, stakeholder inclusiveness,
sustainability context, completeness, accuracy
and comparability. This report is checked against
the GRI G3.1 Framework as Application Level B
and addresses activities and data that fall within
the company’s financial year for the period from
January 1 to December 31, 2011.
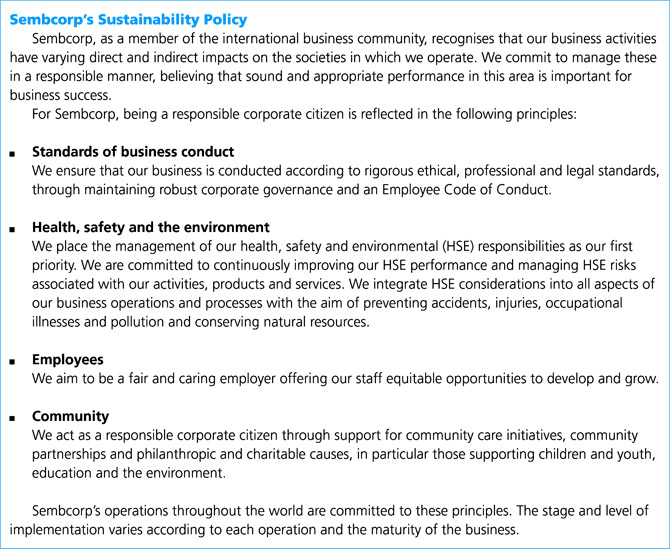
In line with our continuous drive for innovation
and to widen our sustainable business portfolio, the
development of sustainable or green business lines
has become a growing part of our ongoing business.
Our sustainable products and services deliver an
additional competitive edge to our customers,
enabling them to achieve their sustainability and
environmental goals. Our sustainable business
operations include the following:
In December 2011, Sembcorp commenced
operations of our woodchip-fuelled biomass steam
production plant on Jurong Island, Singapore. The
plant produces up to 20 tonnes of steam per hour for customers using waste wood collected from
industrial and commercial waste and processed by
our solid waste collection business. For more details
on the plant, please refer to the write-up
on energy-from-waste solutions below.
Meanwhile, in the UK, the Sembcorp Biomass
Power Station in Teesside uses sustainable wood for
fuel. The 35-megawatt combined heat and power
plant is the first large scale wood-fired renewable
energy plant in the country and saves 200,000
tonnes of carbon dioxide emissions a year.
Sembcorp is Singapore’s first commercial importer
and retailer of natural gas, considered the cleanest
of all fossil fuels. Since 2001, we have been
importing 341 billion British thermal units of natural
gas per day from West Natuna in Indonesia
and supplying it to major power generators and
petrochemical companies. From the fourth quarter of
2011, we started importing an additional 90 billion
British thermal units of gas per day.
Sembcorp aims to apply technology to achieve
greater efficiency and lower emissions in our power,
steam and desalination operations. A summary of
our use of such technologies may be seen in the
table below.
In May 2010, Sembcorp announced a joint
venture agreement with Gayatri Energy Ventures
to build, own and operate a 1,320-megawatt
coal-fired power plant in Andhra Pradesh, India.
While the plant will be fired by coal, it will utilise
supercritical technology which reduces emissions
of carbon dioxide and other pollutants by consuming
less fuel per unit of electricity generated, reducing
its associated environmental impacts. Sembcorp
expects the power plant to be substantially fuelled
by low sulphur non-coking coal.
Sembcorp’s water business is actively playing
a part in providing sustainable water solutions
to meet the growing needs of industries and
communities and support ongoing development
in emerging economies. We supply water to over
five million people worldwide through our municipal
water operations and also support the specialised
water needs of industrial companies while reducing
their impact on the environment.
Sembcorp owns and operates facilities capable
of treating high organic concentration and high
salinity industrial wastewater. Our industrial
wastewater treatment facilities in China and
Singapore are capable of treating wastewater up
to 20 times more concentrated than municipal
sewage and up to 1.5 times more saline than
seawater. By treating our industrial customers’
wastewater to meet discharge standards, we help
industries limit their impact on the environment.
In Singapore, our largest industrial wastewater
treatment plant on Jurong Island is expected to
commence operations in the second half of 2012.
The 9,600 cubic metres per day plant is capable
of treating multiple streams of complex industrial
wastewater and will more than double our current
capacity on the island.
We were the first company in China to be
allowed to treat highly concentrated industrial
wastewater directly from source without requiring
our customers to invest in pre-treatment facilities.
Chinese government regulations require industrial
companies to pre-treat their wastewater to the
standard of municipal sewage before discharging
the wastewater to a standard sewage treatment
plant. The decision to permit industrial companies
to discharge effluent directly to our wastewater
treatment facility signifies a new milestone for
advanced wastewater management in China.
Beyond treating wastewater, Sembcorp also
reclaims water from treated effluent. This integrated
closed loop approach minimises liquid discharge,
conserves precious water resources and offers a
sustainably-sourced alternative water supply to
industries and households. In Singapore, we are
a pioneer in reclaiming industrial effluent on Jurong
Island. In China, we opened our first industrial water
reclamation plant in the Zhangjiagang Free Trade Port
Zone which is capable of reclaiming industrial water
from treated effluent for reuse by industries. Our
industrial wastewater treatment and water reclamation
facilities in the area have been selected by the
governments of Singapore and China as Government-to-Government showcases for bilateral cooperation in
water management, and won prestigious Honour
Awards at both the East Asian and Global International
Water Association Project Innovation Awards in 2010.
Our NEWater plant in Singapore, capable of
producing 228,000 cubic metres per day of water, is one
of the largest water reclamation plants in the world and
plays a significant part in Singapore’s water sustainability
journey. It won the Water Reuse Project of the Year at
the Global Water Awards 2010, which recognises the
water reuse project that represents the most significant
achievement for the industry internationally.
We provide sustainable water supply through
desalination to meet growing water demand. Our
US$1.7 billion plant in Fujairah, UAE and our
upcoming US$1 billion plant in Salalah, Oman,
have a water capacity of 100 million and 15 million
imperial gallons per day of desalinated water
respectively. Both integrated power and desalination
plants use various desalination technologies such
as multi-stage flash and reverse osmosis.
Through Sembcorp’s range of services, waste
that would usually be disposed of in landfills
and incineration facilities is diverted for recycling.
Within the Sembcorp Group, we have capabilities
in advanced waste treatment and resource recovery,
including composting and waste-to-resource. Our
waste-to-resource facilities in Singapore extract
recyclables from waste collected through our waste
collection arm, which is the leading operator in
Singapore serving five out of the nation’s nine
municipal sectors. Sembcorp also operates a
construction and demolition materials recovery
facility in Singapore recovering timber, hardcore
and fines, as well as ferrous and non-ferrous metals.
Waste wood collected is processed and used to fuel
our new woodchip-fuelled biomass steam production
plant to produce steam for our customers.
Furthermore, a comprehensive range of waste paper
recycling services is offered from collection, sorting
and baling to bulk supply of recovered paper to
paper manufacturers.
Sembcorp develops self-sufficient integrated
urban developments comprising industrial parks as
well as business, commercial and residential space.
The business’ integrated approach to delivering
urban work and living environments attracts local
and international investments which facilitate
development, promotes a conducive business
environment and creates jobs for locals.
Sembcorp manages integrated urban
developments with a total gross project size of
7,687 hectares. The integrated developments are
master planned with proper zoning of industrial,
commercial and residential areas, and have strict
effluent discharge guidelines to prevent toxic
discharge into the environment. In addition, on-site
sewage treatment plants treat the effluent before
discharge. Where possible, conservation of the
natural environment and preservation of greenery are
incorporated into the master plans.
Our fourth Vietnam Singapore Industrial Park
development in Hai Phong, Vietnam, incorporates
conservation considerations into its master plan,
with 30% of the land within the development
reserved for green space and preservation of local
flora and fauna. Existing wetlands on the site as well
as tributaries from the Cam River running through
the property will be preserved and made a feature
of the development, while two large retention
ponds will be created to aid water flow during the
monsoon season. These ponds integrate with the
community’s leisure space, while providing a source
of water for landscaping.
Our joint venture project in China, Sino-Singapore Nanjing Eco Hi-tech Island, is envisioned
as a world-class integrated urban development
on a green island which will have more than
50% of its area preserved for eco-tourism. It will
also feature an exhibition centre and a research
and development park with green roofs to alleviate
urban heat effect as well as rain collection canopies.
Wetland biofilters and park connectors are also
incorporated into the integrated development’s
overall design plan.
In 2011, we added a new development to our
portfolio, the 1,000-hectare Singapore-Sichuan
Hi-tech Innovation Park in China. With the promotion
of research and development, high-tech upgrading
and environmental protection among the central
government’s twelfth “Five Year Plan” objectives,
the park will focus on technology-driven, knowledge-intensive
industries and showcase a modern,
innovative and low carbon emission city.
Sembcorp recognises that its business operations
are intertwined with various stakeholders. In early
2012 we conducted a stakeholder engagement
planning exercise in line with AA1000 Stakeholder
Engagement Standard with the help of an
independent consultant to review and identify
our key stakeholder groups.
Sembcorp’s key sustainability stakeholder
groups have been identified as shareholders,
financial institutions, the investment community,
government, regulators, customers, employees and
members of communities where we have operations.
Our internal stakeholders are crucial in our
day-to-day practice of sustainability and in
determining our sustainability-related risks and
identifying areas for future improvement. As part
of our efforts to create a culture of open two-way
communication, employees are encouraged to
contribute ideas on improving workplace
practices and the delivery of products and
services. This includes feedback on issues such
as dishonesty and fraud via our whistle-blowing
scheme and confidential feedback channels. To
further promote sustainability as a part of
Sembcorp’s corporate culture, employee appraisals
take into account HSE performance as appropriate.
For further information on employee engagement, please click here.
Sembcorp maintains open communication
channels with the investment community including
shareholders, analysts and potential investors. We
actively engage our stakeholders through various
platforms such as one-to-one meetings, group
meetings, presentations and site visits. In 2011,
we had over 130 meetings with the investment
community. Further information on such
communication can be found in the Corporate Governance and Investor Relations chapters.
We engage in regular dialogues with the
government, regulator and community through
different platforms such as meetings, briefings and
presentations. For example, our solid waste
management operations in Singapore hold monthly
meetings with the respective town councils of every
municipality that we serve.
We proactively engage with customers to find
out how we can improve our services. In the UK,
focus groups and internal surveys are conducted
annually to find out how our municipal water
operations can enhance or improve our service
offering. These also help identify key drivers of
satisfaction, so we know where to focus our efforts
and investment. All feedback is used to make
improvements either via training of advisors,
enhancements to existing processes or the
development of new service enhancements. Our
operation in Bournemouth, UK, is currently
developing a framework to form a customer
engagement panel for the next review of prices by
the regulator. In Singapore, our Utilities operations
conduct a bi-annual survey with its gas, power and
utilities customers. The online survey is sent to all
customers, and in 2010, the overall customer
satisfaction rate was 95%. Aside from the survey,
customers have access to an online portal to retrieve
their consumption information, and they can provide
further feedback via email or a hotline telephone
number. Our solid waste management operations
also conduct an annual online survey with its
customers, and provide a hotline number as well as
an email address for further feedback.
Through these and other formal engagement
programmes, we aim to continue to align relevant
stakeholder issues with our overall strategy.
Sembcorp has a complex supply chain and our
actions influence many businesses along the value
chains we operate in. Many clients are in the process
of developing their own sustainability programmes. As
a provider of essential solutions, we aim to assist our
customers to improve their HSE performance, limit
their environmental impact and conserve resources.
As a provider of utilities, Sembcorp directly
consumes primary resources, produces waste and
emissions and manages people, buildings, treatment
processes and machinery. As such, we work closely
with our suppliers, business partners and contractors
to ensure adherence to our Group HSE guidelines.
All suppliers are subject to a vendor pre-qualification
review that includes checks on its HSE provisions. We
ensure that the appointment of all vendors and
contractors comply with the applicable government
certification requirements as well as our guidelines
and policies. Platforms such as safety induction
programmes and contractor HSE engagement help
to actively identify gaps and improve performance.
In Singapore, where over 70% of Sembcorp’s
contract workers are employed, we require
contractors to comply with all requirements stated
in a Permit to Work application, issued by the
Ministry of Manpower, before they can work in our
facilities or operating sites. This includes requirements
for health and safety provisions and the submission
of proper paperwork to demonstrate the presence
of adequate workers’ compensation insurance
coverage, as well as relevant resident visa and work
permits. Employees of our contractors must also
attend HSE training before any work is started.
At Sembcorp, we recognise the importance
of being an active player within our industry and
engaging with our peers and the wider business
community on sustainability issues. Sembcorp is a
founding member and supporter of the Singapore
Compact for Corporate Social Responsibility,
a national society promoting sustainability issues
in Singapore.
Our Group President & CEO also serves as a
member of Singapore’s Climate Change Network,
a forum started by Singapore’s National Climate
Change Secretariat. The network serves as a
platform for representatives from various sectors
to nurture dialogue on climate change matters and
to exchange information on climate change issues.
At the industry level, Sembcorp participates in
the Responsible Care voluntary initiative, endorsed
by the Singapore Chemical Industry Council (SCIC).
This encourages members to adopt 10 guiding
principles for a safer chemical industry through
the six management practices of employee health
and safety, distribution, pollution prevention,
process safety, product stewardship and community
awareness, and emergency response. Our Utilities
business in Singapore has actively participated in a
number of industry workgroups organised by the
SCIC looking at issues such as capacity building on
process safety and drafting new quantitative risk
assessment guidelines.
In Singapore, Sembcorp is also a member of
the Sakra Island Community Awareness Group,
which seeks to promote community awareness
and a standardised management practice code for
emergency responses among companies located
in the Sakra district on Jurong Island. Similarly,
our Teesside, UK operations are active in the North
East of England Process Industry Cluster which serves
as a unified voice for the process industry in
Northeast England, where a substantial part of the
UK’s chemical, petrochemical, speciality chemical,
pharmaceutical, polymer and biotechnology
industries are based. In the UAE, our operations in
Fujairah are part of the Abu Dhabi Water & Electricity
Authority’s task force in formulating HSE procedures
and guidelines for the energy sector.
In 2011, Sembcorp received both national and
global recognition and a number of awards for its
efforts to promote and practise sustainability.
Sembcorp has been selected as an index
component of the Dow Jones Sustainability Asia
Pacific Index for 2011. The index represents the top
20% of the largest 600 companies in the Asia Pacific
developed region based on long-term economic,
environmental and social criteria. Sembcorp is
honoured to be one of only four Singapore
companies selected for the index.
Sembcorp clinched the coveted Gold award
for Best Annual Report (for companies with
S$1 billion and above in market capitalisation) at
the Singapore Corporate Awards 2011 for our
Annual Report 2010, in recognition of our excellence
in reporting and disclosure. The prestigious awards
showcase excellence in corporate governance and
shareholder communication, and the Best Annual
Report award was introduced to encourage social
responsibility reporting as well as increase the
awareness of the organisations’ responsibility to
the community.
Sembcorp won the Frost & Sullivan Asia Pacific
Waste Recycling Company of the Year award in
2011, in recognition of our excellence in solid
waste recycling, waste treatment support and
applying environmentally-friendly waste recycling
technologies in our businesses. The award also
recognises the company’s position as a major
industry player providing waste recycling services
across customer verticals, and our ability to
successfully respond to our customers’ needs
with a business strategy that incorporates best
sustainable practices.
Sembcorp was named the Most Transparent
Company (multi-industry / conglomerates category)
at the Securities Investors Association (Singapore)
Investors’ Choice Awards 2011 for the third year
running. This recognises our continuous drive
towards transparency and good governance,
and our efforts to give stakeholders an accurate,
coherent and balanced account of our company
and performance.
Sembcorp was conferred top honours at the
Singapore Sustainability Awards 2011, winning the
Sustainable Business Award (Enterprise category).
The awards, presented by the Singapore Business
Federation, recognise local enterprises with
outstanding sustainable business practices.
Companies are assessed on their innovation,
corporate social responsibility, commercial potential
and sustainable business growth, as well as their
environmental, health and safety and production
process management systems.
Sembcorp was honoured by the SCIC with gold
awards in the categories of Community Awareness
and Emergency Response and Pollution Prevention,
and three achievement awards in Distribution,
Employee Health and Safety and Process Safety at
the Responsible Care Awards 2011. The awards
honour companies who have incorporated
Responsible Care management practices into their
operations and recognise those with exemplary
performance in maintaining high HSE standards.
In recognition of our continuing efforts
to provide water and sanitation services of the
highest quality, both Sembcorp’s South African
operations were awarded the prestigious Blue
Drop and Green Drop status in 2011 by the
Department of Water and Environmental Affairs.
Only 7.2% of all water systems in South Africa
were awarded the Blue Drop (drinking water quality
management) status in 2011, while the Green Drop
(wastewater quality management) status was
achieved by only 4.7% of South Africa’s wastewater
systems. In addition, one of our operations was
conferred the Platinum status for achieving the
Blue Drop status for three consecutive years, making
it among just 10 operations in the country to be
awarded Platinum.
HSE issues are clearly linked to Sembcorp’s
long-term success and have been identified as
material factors in terms of their potential impact on
our business operations. In managing our HSE issues,
we continue to be guided by four main principles:
• |
Implementing internationally recognised HSE
management systems such as ISO 14001:2004
and OHSAS 18001:2007 |
• |
Actively investing in financially viable
sustainable business lines, which form part of
our core operations |
• |
Using continuous improvement to enhance
HSE performance of our processes, products
and services |
• |
Working closely with our business partners and
seeking active engagement to promote mutual
HSE performance improvement |
Sembcorp’s operations are in various phases of
development. They include facilities that are under
construction, newly commissioned as well as recently
acquired. As such, our priority continues to be on
aligning and improving standards across the Group and proactively managing HSE performance
throughout the asset management life cycle,
from business development and project conception,
to operation and the end of the asset life.
With operations that spread across six continents,
our Group HSE department is the driver of our
management systems and coordinates our global
HSE efforts. Management committees and reporting
structures have been established with regional
coordinators working closely with the department.
This ensures the effective management of HSE issues
with the purpose of setting long-term HSE objectives
and targets and complying with regulatory
requirements, voluntary group guidelines, standards
and initiatives. Reporting to the Board Risk
Committee (BRC) was formalised in 2011, and HSE
issues have been incorporated into regular reports
to the board with key HSE risks and controls also
presented to the BRC.
The key goal for the Group HSE department in
2011 was to strengthen overall Sembcorp Group HSE
culture, create more HSE awareness and shape the
development of the HSE management framework
across the Group. The framework outlines the roles
and responsibilities of various relevant departments and business units, in line with the Group HSE policy. The Group HSE policy can be viewed on our website at www.sembcorp.com.
The framework was endorsed by the BRC and
implemented across all Utilities businesses in the
Group. Periodic HSE assurance audits help to ensure
that HSE matters are managed professionally in order
to meet legal compliance and ensure continuous
improvement in all our activities.
In an effort to standardise HSE guidelines and
reporting, Group HSE has reviewed and developed
a standardised set of reporting parameters to track
and monitor key HSE statistics across the Group.
The new parameters and template are based on
the Sembcorp 4/0 targets. The 4/0 targets refer to:
zero harm to people, zero damage to the
environment, zero damage to assets and zero
non-compliance to legal and regulatory requirements.
Along with the Group HSE guidelines, the 4/0 targets
and reporting parameters were approved by the
BRC in February 2011.
It is compulsory for all business units under the
operational control of the Sembcorp Group to follow
these guidelines.
A Group HSE workshop is conducted annually
where employees from our operations around the
world will meet and contribute ideas towards the
formulation of key HSE initiatives as well as a set of
global mandatory HSE guidelines for all business
units under our operational control.
In addition, in 2011, Group HSE also conducted
an inaugural HSE workshop for Sembcorp’s China
operations, with the objective of promoting HSE
awareness and best practice. This resulted in the
establishment of a China HSE Committee comprising
representatives from each site, providing a platform
for HSE colleagues in China to communicate,
share best practices and support improvements in
HSE. Moving forward, Group HSE and Group
Asset Management will support the coordination
of a regular asset management and HSE workshop
to support China’s operations and its HSE
performance improvement.
Group HSE conducts regular HSE audits for
the operations to achieve continuous improvement.
In 2011, we covered our operations in Fujairah,
UAE, and three facilities in China. The audits were
conducted in accordance with Group HSE guidelines,
to help identify and bridge gaps so that these
business units can improve on their HSE
performance. Our water operations in China have
also embarked on automating their reporting
of HSE and operational statistics through
collaboration with the Group HSE and Group
Performance Management departments.
Sembcorp’s two greenfield projects in India
and Oman are in the construction and commissioning
phases respectively. Group HSE works closely
with their counterparts at the new plants to share
and communicate Group HSE guidelines and
requirements. The team visited the plant in Oman
for a two-day HSE review in November 2011, and
established an understanding of the plant’s HSE
management system framework and existing HSE
practices. Potential areas for improvement were
identified and recommendations were made for
establishing HSE procedures and processes.
We continue to work towards implementing
internationally recognised HSE management systems
across our operations.
In early 2012, Sembcorp Gulf O&M Company in
the UAE underwent a certification audit for both ISO
14001 and OHSAS 18001 and was awarded both
certifications with zero non-conformities. Following
these certifications, we will be working towards the
additional requirement of attaining the Abu Dhabi
Environment, Health and Safety Management System
qualification, for which assessments will conclude by
end 2012.
Meanwhile, Sembcorp Utilities Singapore
obtained the integrated OHSAS 18001 and ISO
14001 Environmental Management System in
March 2011.
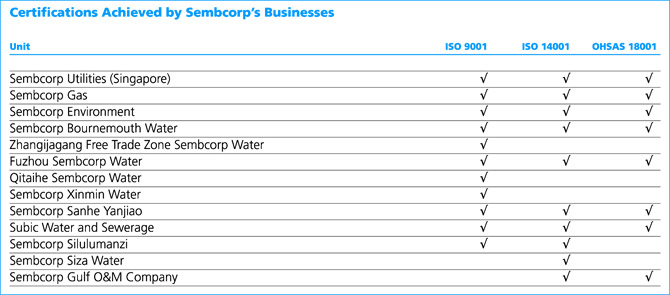
As a key player in the energy and water sector,
we are keenly aware of global climate change issues.
We aim to limit and manage the impact of our
operations on the environment by enhancing our
efficiency and investing in assets which apply
technologies to manage and reduce emissions. For
example, our new woodchip-fuelled biomass steam
production plant in Singapore produces process
steam for third-party commercial customers. The
plant was designed to the Building and Construction
Authority’s Green Mark Gold standard, and
incorporates natural ventilation and lighting, solar
power and recycled building materials.
Environmental studies including environmental
impact assessments are a part of Group HSE’s
requirements for new major projects and expansions.
Environmental impact assessments are carried out in
accordance with national and / or international
standards and methodologies. All recommendations
put forth from the assessments form part of our
management of HSE risks and are incorporated in the
planning, design, construction and commissioning of
the new plants. Other environmental assessments
such as environmental baseline studies and pollution
control studies are conducted as required in the
relevant countries.
In 2011, we have included data on our
environmental management from our operations
in Singapore, China, the UAE, UK and Vietnam. We
continued to track our primary energy sources usage.
Natural gas still accounts for the largest proportion
of our fuels used. We also monitored indirect energy
usage in the form of electricity consumption by our
operations within the scope of the report.
We are proactive in seeking to reduce our energy consumption and corresponding greenhouse gas emissions through investing in energy efficient and renewable energy technologies. In Singapore, our energy-from-waste technology, which converts organic waste into biogas, has led to a reduction in the consumption of over six million megajoules of natural gas. In Bournemouth in the UK, our operations used 244 megawatt-hours less of grid electricity compared to the previous year. Standby generation was also reduced, saving 6,028 litres of
gasoil which led to a reduction of over 150 tonnes of carbon dioxide emissions. Photovoltaic cells will be installed to generate clean electricity for the plant. In addition, pumps will be refurbished to ensure efficiency during operation. For a summary of the energy efficiency technologies which we apply in our operations, please click here.
Our carbon dioxide emission estimate1 is derived
from stationary fuel combustion and does not cover
process emissions. In 2011, our carbon dioxide
emission amounted to over 6,500 kilotonnes as
compared to over 7,600 kilotonnes in 2010. Our
emissions estimate is based on the World Resource
Institute / World Business Council for Sustainable
Development Protocol as well as site specific data.
1 Emission data excludes plants in China which are not stationary fuel combustion plants
In addition to carbon dioxide and greenhouse gas
emissions, we monitor emissions of sulphur oxides
(SOx) and nitrogen oxides (NOx). The data tracked is
from our energy generation operations in Singapore,
the UAE and UK. Our operation in Teesside is the main
contributor of SOx and NOx due to its use of coal.
Our water business has grown significantly over
the recent years through acquisitions and organic
growth. We provide services ranging from specialised
industrial wastewater treatment to water reclamation,
desalination and the supply of potable and industrial
water. Sembcorp manages facilities capable of
producing and treating over seven million cubic
metres of water and wastewater daily and serves
over five million people worldwide. Through
innovation, we make every effort to ensure the
efficient use and reuse of water resources.
As part of the water solutions we offer to our
customers, we treat and supply water extracted
from surface water, groundwater (including lakes,
rivers, oceans and aquifers) as well as public utilities
(including wastewater). In 2011, our operations
in Singapore, China, the UAE, UK and Vietnam
extracted over 1,500 million cubic metres of water
primarily for treatment, supply to our customers
and use in our operations. Out of the total water
extracted, 91% was surface water, 4% was
groundwater, 3% was wastewater and 2% was
water from public utilities.
In 2011, Sembcorp recycled almost 20 million
cubic metres of water, or over 1% of our total
volume used, for supply to our customers and use
in our operations, reducing the intake of potable
or raw water supplies and also helping our customers
to reduce the amount of raw water needed for
their operations.
The graph below shows our potable water use
and the amount of water recycled.
Sembcorp received numerous awards in 2011
for its water services, including being named Water
Company of the Year at the prestigious Global Water
Intelligence’s Global Water Awards. This award
recognises Sembcorp as the water company that has
made “the most significant contribution to the
development of the international water sector in
2010”. Further information on the awards won by
Sembcorp in 2011 can be found here.
As one of the largest solid waste management
players in Singapore, Sembcorp provides services that
aim to reduce waste going to incineration or landfill
facilities. We also promote waste reduction by
encouraging recycling. In line with our business focus
to reduce waste for disposal, we are actively
developing differentiating know-how including
energy-from-waste capabilities. Our woodchip-fuelled
biomass steam production plant began full
commercial operations in late 2011, and is the first
such energy-from-waste facility in Singapore to
produce renewable process steam for third party
commercial customers on Jurong Island.
Our Group HSE guidelines require that any
uncontrolled and / or unauthorised discharge of
substances or any spill and / or leak of 500 litres or
more without secondary containment is reported.
There were no reportable spills or leaks in 2011.
An enhanced set of HSE reporting parameters
including the Sembcorp 4/0 targets was agreed upon
in February 2011 for application across all business
units in Singapore and overseas.
Using indicators of accident frequency rate (AFR)
and accident severity rate (ASR), in accordance with
the tracking criteria set by Singapore’s Ministry of
Manpower, the safety performance from our Utilities
operations in Singapore, China, the UAE, UK and
Vietnam has been recorded.
Our Utilities operations, excluding solid waste
management, reported 14 lost time injuries and
19 first aid cases in 2011, plus 166 man-days lost
in 2011 (0.01% of the total man-hours worked)
due to injuries sustained by our employees and
contractors during operations.
Our employees are monitored for noise induced
hearing loss and dermatitis and no case of either
incident was reported in 2011.
The solid waste management business’ safety
performance in Singapore is reported separately
from the performance of the rest of our Utilities
operations. This is due to the fact that the solid
waste management business’ waste collection
operations employ manual labour to a greater degree
and therefore have a different risk profile from our
energy, water and on-site logistics operations.
Our solid waste management business in
Singapore saw an increase in the AFR from 6.4 in
2010 to 10.6 in 2011. However, its ASR decreased
from 346.9 in 2010 to 148.3 in 2011. Safety remains
important to us and our solid waste management
business has taken preventive action to improve its
AFR and ASR levels. This includes ‘toolbox meetings’
with management and employees to cover the
importance of health and safety and spot inspections
at operational sites. In addition, monthly briefing
sessions are organised to allow employees to share
their lessons learnt in managing safety in their work.
Sembcorp’s solid waste management business in Singapore operates a fleet of 200 commercial
vehicles and our staff undertake a considerable
amount of driving each year. One of our key safety
indicators for this business is vehicle accidents. In
2011, there was a substantial decrease in the
accident rate both in terms of absolute numbers
(89 in 2011 compared to 137 in 2010) and number
of incidents per 100,000 kilometres driven (0.7 in
2011 compared to 1.1 in 2010).
In January 2011, in addition to the stringent
selection process in the recruitment of drivers,
the company also commenced a safety training
programme for our waste collection truck drivers
in Singapore. This has improved their road safety
awareness and defensive driving ability to reduce
accident rates.
All our products and services are assessed
according to internationally recognised HSE and
quality management systems. HSE and quality
internal audits are conducted regularly to ensure
that the quality of our water supply meets legal and
product specifications. For the list of certifications
achieved by Sembcorp’s businesses, please click here.
At Sembcorp, we recognise that our employees
are our most valuable asset and a key stakeholder
group. We are committed to providing a fair, diverse and
inclusive workplace, and to continuous improvement in
our human resource and people development practices.
Sembcorp strives to maintain a fair, diverse and
inclusive workplace for all its employees. At the end of
2011, there were over 5,000 permanent employees in
the entire Sembcorp group, excluding employees from
the Marine business. 11% of our total headcount
were contract employees. Please see the charts below for the distribution of all Sembcorp’s
permanent employees, excluding employees from the
Marine business, by age, geographical region, gender
and education. Any deviation from this scope is noted
under the individual sections.
With our headquarters based in Singapore, the
Group subscribes to the Principles of Fair Employment
formulated by the Singapore Tripartite Alliance for Fair
Employment Practices and has endorsed the Tripartite
Alliance’s Employers’ Pledge of Fair Employment
Practices. These principles, embedded into our human
resource practices and implemented by Sembcorp on
a global level, include a commitment to:
• |
Recruit and select based on merit, such as skills,
experience and ability, regardless of age, race,
gender or family status |
• |
Treat employees fairly and with respect and
implement progressive human resource
management systems |
• |
Provide equal opportunities for training and
development based on employees’ strengths and
needs, to help them achieve their full potential |
• |
Reward fairly, based on ability, performance, contribution and experience |
• |
Abide by labour laws and adopt tripartite guidelines which promote fair employment practices |
The significantly higher proportion of male
employees in Sembcorp’s headcount is consistent
with industry norms, where the nature of work
required in plants involves more physically demanding
tasks. Sembcorp ensures that equal opportunity is
given to all female employees across the Group.
The staff distribution of non-executive staff
by gender is 12% female and 88% male. The
distribution of staff by gender for executives is
28% female and 72% male.
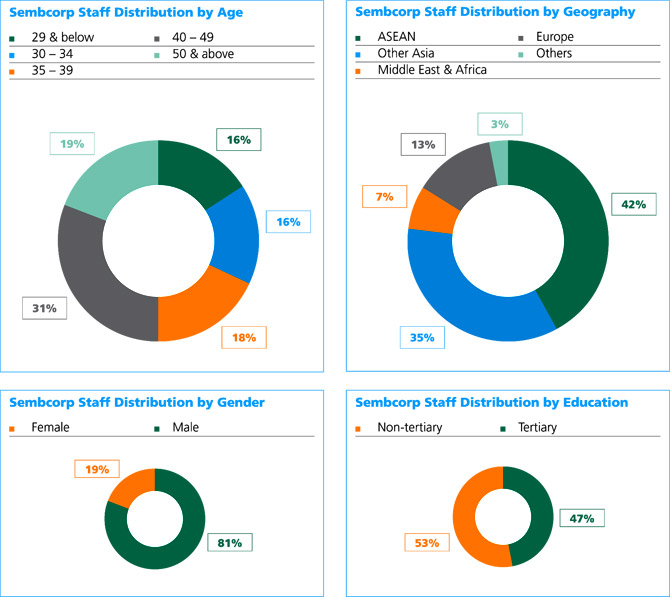
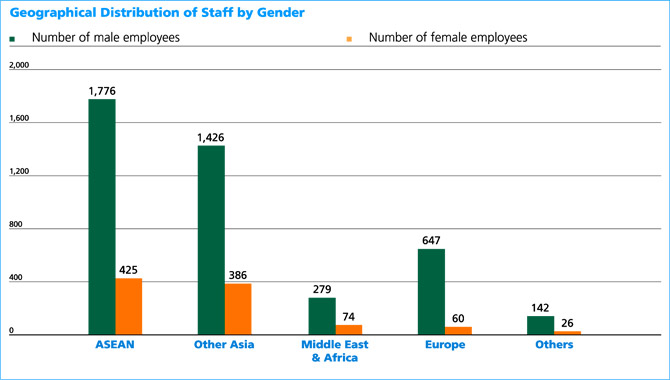
Sembcorp fully supports the basic principles
of human rights and has implemented a number
of policies throughout the Group in support of these
principles, including fair employment practices and
a grievance and harassment policy.
A key tenet of Sembcorp’s business ethics is strict
respect for labour laws within each of the countries
we operate in, all of which preclude forced or child
labour, and is further supported through our policies
and employment practices. The technical nature of
our operations requires an experienced workforce,
both within the organisation and in our supply chain,
as specialist skills are required.
Sembcorp continues to promote a holistic and
balanced lifestyle for our employees, which we
believe is good for both their physical and mental
health. We encourage employees at our various
business units to participate in employee recreation
activities throughout the year, including community
outreach and volunteering initiatives, team sports
events, talks, gatherings and employee family days.
Some of these activities welcome employees to
participate with their family members, such as our
Sembcorp Family Day in Singapore and Fujairah.
Sembcorp also organises an annual Health
Week, a company-funded health education initiative
that helps equip employees in Singapore with
essential health knowledge and personal lifestyle skills.
We recognise the importance of engaging with
our employees and have various platforms through
which we communicate with and receive feedback
from our staff. We provide information on our financial
and business performance as well as on applicable
company standards and policies to our staff. Interactive
staff communication sessions with management are in
place to ensure two-way communication between the
company and its employees.
In 2011, we continued to hold employee briefing
sessions in conjunction with the company’s quarterly
financial reporting cycle. At these sessions, senior
management provides employees with information
on the company’s performance and key
developments. Presentations are also held to brief
employees on topics such as corporate social
responsibility or specific company policies such
as fraud management.
We continue to hold an annual communication
forum in Singapore for managers from Sembcorp
offices all over the world, with detailed briefings from
top management and external experts on our Group’s
operating environment, performance, outlook and
strategy. This forum incorporates an interactive
networking and question and answer session.
Furthermore, at the country level, some business
units also hold quarterly learning and sharing sessions,
senior manager briefings and staff consultation group
sessions. At Sembcorp Bournemouth Water in the UK,
there is also a staff consultative group made up
of elected staff representatives and management
representatives, which meets quarterly to discuss
relevant employee issues.
Over the course of the year, we continued to
communicate corporate updates and business
milestones to all staff through employee emails and
bi-monthly e-newsletters. Relevant and up-to-date
information on staff welfare and benefits was also
publicised to employees via the company intranet.
Sembcorp welcomes feedback from its employees
and provides confidential channels through which
employees can submit feedback and staff
suggestions, including an easily accessible online
channel on the employee intranet. All feedback is
sent to the Group Human Resource department and,
if sent via the internet, is also automatically copied to
the Senior Vice President of Group Human Resource
and the Group President & CEO’s office.
In line with our commitment to high ethical
standards and good corporate governance practices,
we have in place a group-wide whistle-blowing policy
and encourage all employees to report any possible
improprieties on a confidential basis without fear of
recrimination. We have an easily accessible whistle-blowing
link on our company intranet and employees
may also provide feedback via email, mail or fax.
Within the boundaries of each of the jurisdictions
under which we operate, Sembcorp employees are
entitled to practise freedom of association in the
workplace. Sembcorp’s operations span six
continents where labour relations, regulations and
practices differ widely. In 2011, 42% of Sembcorp’s
employees were union members.
Sembcorp maintains excellent labour
management relations with its unions, and holds
constructive ongoing exchanges with employee
unions in its various locations. In Singapore,
Sembcorp is committed to working closely with
the Building Construction and Timber Industries
Employees Union (BATU) as well as the Union
of Power and Gas Employees (UPAGE). Our re-employment
policy, endorsed by BATU and UPAGE,
gives medically fit employees the option of
continuing on their jobs beyond the statutory
retirement age. In an event organised by BATU and
Sembcorp, the Prime Minister of Singapore visited
our Bukit Merah Depot on the first day of Lunar New
Year in 2011 to show appreciation to the workers
who continued to work tirelessly and perform vital
duties on this public holiday.
In the UK, Sembcorp Bournemouth Water has a
long standing relationship with its recognised unions
GMB and Unison. Both unions sit on Sembcorp’s staff
consultative group and the health and safety
committee, where they also participate in safety
inspections. At our Teesside operations, discussions
with Unite (the UK’s biggest union) are conducted in
line with our collective ‘Together Agreement’ which
covers over 90% of our employees at this operation.
Formal joint consultation meetings with employees
and unions are conducted three times a year, and
meetings between management and the company’s
senior union representatives are held bi-monthly.
Sembcorp’s success is driven by the calibre and
performance of its people. We recognise that it is
essential to equip our employees across all levels of
seniority to meet the changing needs of the
marketplace. Sembcorp offers employees a range of
personal and professional development opportunities
including career development, education, talent
management and leadership programmes.
In 2011, the Group continued to invest in
competency building for our employees, spending
over S$1.5 million on training for employees within
our operations in Singapore, China, the UAE and UK.
It is a priority for us to enhance the skill level
of our employees to ensure smooth succession.
Sembcorp’s learning and development programmes
factor in issues such as succession planning and
addressing skill gaps with relation to core
competency requirements.
Around 5% of our non-executive staff worldwide
are due to retire in the next five years, and a further
7% in the next six to 10 years. Around 2% of our
executive staff worldwide are due to retire in the next
five years, and a further 5% in the next six to 10 years.
The Sembcorp Leadership Competencies
programme is our unique talent management and
development system that defines the qualities and
performance expectations of a Sembcorp leader.
Capable leaders are crucial in achieving business
success and the Sembcorp Leadership Competencies
detail the ways in which Sembcorp leaders should
act and respond. Managers also attend courses
to enhance their presentation, negotiation,
communication and coaching skills as well as
courses on building and leading high-performance
teams. Senior executives are expected to undertake
regular training to update and upgrade their
skills and education programmes are accessible to
them at prestigious institutes such as the Harvard
Business School, INSEAD and the Temasek Business
Leadership Centre.
We offer employees the opportunity to
experience different cultural and operational settings
through job rotations and attachments. We currently
have more than 50 employees of different
nationalities posted from our Singapore office to
various overseas businesses. Internships and industrial
attachments also provide students and Sembcorp
scholars with practical experience and exposure to
our operations while they undergo their studies.
We send our employees for professional training
to allow them to develop skill sets that better equip
them for their roles. Working with local educational
institutions in Singapore, we send our engineers to
specialised technical competency courses. Our
employees are also sent for professional training
related to the industry, including courses under
Singapore’s National Skills Recognition Scheme and
Workforce Skills Qualification scheme under the
Workforce Development Authority.
In Singapore, staff are also encouraged to
pursue higher qualifications which are sponsored
by the company.
In the UK, our operations are signed up to the
‘Investors in People’ standard, the UK’s leading people
management standard. This provides a business
improvement tool to help organisations develop
performance through their people. Both our operations aim to provide education and training
for all employees to carry out their duties and provide
them with appropriate opportunities for development.
This involves identifying skill gaps in accordance with
core competencies. Sembcorp is also helping to shape
the future of the industry by proactively engaging in
training and skills development throughout the
northeastern region, as well as raise the performance
bar of apprentices and other workers in the industry.
As an industry leader in various sectors,
Sembcorp encourages our employees to share
and exchange best practices through platforms
such as seminars and conferences on a local
and international basis. In the UK, our Senior Vice
President of Regional Human Resource sits as the
Chairman of the North East Regional Skills Board for
the National Skills Academy for the Process Industries
and uses his expertise to improve the skills of the
existing workforce as well as attract and retain new
entrants to the industry.
Sembcorp has implemented a system for
performance appraisals across its operations in all
countries. The appraisal system allows all employees
to comment on their personal contribution
throughout the year and to jointly identify areas for
further career development and learning with their
supervisors on a regular basis. It enables constructive
discussion and uses the feedback process to ensure
that employees share the responsibility for managing
their career and goals. The appraisal process
incorporates shared future objectives to ensure that
employee outputs are also aligned to the needs of
the business. Selected senior managers are also
assessed using a 360-degree appraisal system where
feedback is sought from a range of superiors, peers
and colleagues and other partners. The profile of
essential competencies for the job function compiled
from this process is also incorporated into these
managers’ development plans, helping them lead
their teams successfully and enhance their
professional performance.
Rewarding performance is the key component
of Sembcorp’s employment retention strategy.
The Group offers competitive base pay packages
throughout our global businesses that are based on
country-specific conditions. Rewards include annual
salary increments and annual performance bonuses,
as well as longer-term incentives linked to sector
practices and based on the performance of the
Group, the company and the individual.
Share-based incentives, administered by a board
nominated committee, remain a key component
of the Group’s pay structure and are deliberately
aligned to long-term Group performance objectives.
Since 2007, share options granted to staff have been
replaced with restricted shares. This Restricted Share
Plan applies to employees of the Group, while the
Performance Share Plan is primarily for key executives
of the Group.
All employees are eligible for comprehensive
insurance coverage on a global basis. They can join
the company’s private medical and dental insurance
scheme under which the company meets the cost of
employee membership and allows employees to
include eligible dependants. The company also
provides additional insurance cover for life, travel,
personal accidents, workers’ compensation and
hospitalisation and surgical expenses.
Sembcorp maintains an ongoing commitment
to support the local communities in which we
operate through supporting social development and
community investment projects. In 2011, Sembcorp
contributed over S$1.3 million in cash and in-kind
support to its communities (excluding community
investment initiatives by our separately listed Marine
business). We took part in many initiatives in our communities in support of children and the elderly,
education, the environment and sports and fitness.
Our employees are active volunteers in the
community, providing helping hands as well as
management expertise. 48% of our operations
have local community engagements and
development programmes.
Our employees offer their time to volunteer in
a number of initiatives that the company organises.
For example:
• |
Sembcorp has been a supporter of Singapore’s
Assisi Hospice (which provides palliative care for
people with life-limiting illnesses) since 2008.
Sembcorp volunteers help with the running of
the charity’s Fun Carnival, which generated more
than S$800,000 in donations in 2011, as well as
its Christmas carnival, bringing goodwill and
cheer to the patients. |
• |
For the third year running, Sembcorp has
partnered with the Sunshine Welfare Action
Mission (SWAMI) in Singapore to bring festive
cheer to needy elderly households. SWAMI is a
non-profit organisation providing nursing care
and shelter for the sick, aged and handicapped
from needy backgrounds. In the run-up to the
Lunar New Year in 2011, SWAMI identified 23
households whose residents do not have the ease
of movement, to benefit from volunteers spring
cleaning their homes. |
• |
In the UK, Sembcorp employee Jane Atkinson
was granted an honorary doctorate in Business
Administration by Teesside University, one of the
leading UK universities for engineering, in
recognition of her work in championing
engineering education among youths. |
Sembcorp supports projects that help
communities, such as:
• |
In 2011, Sembcorp, through its joint venture
in the Vietnam Singapore Industrial Park,
launched the first community clinic in Binh
Duong. With a medical team from My Phuoc
Hospital, this clinic provides free first aid,
medical consultation and counselling services
for the medically underserved populations
of Binh Duong province. |
• |
In China, our Yancheng operations organised
their fifth ‘Water Services For The Community’
event in the Chaoyang district to promote the
accessibility of municipal water for all. The event
helped facilitate water maintenance and repair
services for the residents, and also generated
greater awareness on water conservation, quality
and pricing. |
• |
In South Africa, Sembcorp Siza Water donated
an immune haematology test machine to a local
non-governmental organisation HIV / AIDS centre
to help overcome traveling and cost barriers
to getting tested. |
• |
Sembcorp Bournemouth Water has been a
supporter of international charity WaterAid. In
2011, Sembcorp Bournemouth Water received
The President’s Award, endorsed by WaterAid’s
President, His Royal Highness The Prince of Wales,
for its support over the last 30 years. |
• |
Our operations in Teesside extended their
professional expertise to a neighbouring village
to help secure lower costs with the building
suppliers for the renovations of their historic
village hall. |
• |
Sembcorp Utilities Chile worked with local
community leaders to pilot a campaign in two
Santiago regions, entitled ‘Yo cuido mi grifo’ (I take care of my fire hydrant), to educate the
local community about the importance of fire
hydrants. The project also saw the opening of
two children’s water parks. The project resulted in
savings of over 600,000 litres of water a day. |
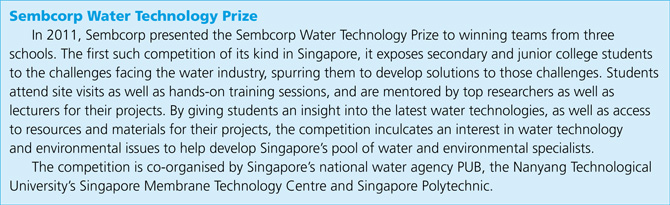
Sembcorp also contributes to programmes
supporting wildlife and biodiversity. We continue
to support the Sembcorp Forest of Giants in the
Southern Ridges through donations to the Singapore
National Parks Board’s registered charity, the Garden
City Fund. In 2011, we further developed the
programme to promote greater awareness and
appreciation of nature. Sembcorp volunteers were
trained to be guides of the Southern Ridges, which
span the hills of Mount Faber Park in Singapore.
Sembcorp’s municipal water operations in
Bournemouth, UK, continues its long-standing
support of the Dorset Wildlife Trust which manages
more than 40 nature reserves in the county. In 2011,
Sembcorp Bournemouth Water provided support to
the charity to restore areas of chalk streams that have
been affected by human intervention. The crystal
clear waters of chalk streams support more wildlife
than any other waters in Britain, with a huge range
of aquatic insects, spawning sites for trout and
salmon and food for predators.
For further information on sustainability at Sembcorp Industries, please visit our website at www.sembcorp.com. If you have any comments or wish to discuss any of the contents of this report or other sustainability issues, please contact:
Group Corporate Relations
Tel: +65 6723 3113
Email: [email protected] |
|
|
|
|
|